Research
home
Fundamental Research for Producing High-Purity & High-Cleanliness Stainless Steels
Refining of High-Mn Steels for Generation Applications
Applications of Computational Thermodynamics for Producing High-Clean Steels ; Focusing on Smart Manufacturing
Novel Manufacturing Processes for Advanced High-Entropy Alloys
Grain Refinement of Macro-& Microstructure of Steels using Non-Metallic Inclusion
Zn-AI-Fe Dross Formation Mechanism in Hot Dip Galvanizing Bath for Producing Advanced Automotive Sreels
Physical Chemistry of MnO-base Slags for Producing High-Functional Manganese Ferroalloys
Viscosity-Structure Relationship of Molten Slags and Glasses
High Temperature Physical Chemistry of Metals and Slags
Characterization of Chemical Reactions at Slag-Refractory Interface in High Temperature Reactors
Extraction and Purification of Titanium and Its Alloys
Physical Chemistry of Molten Salts for Producing Magnesium and Zirconium
Recovery of Precious- & Rare Metals from Electric Wastes and Industrial By-products ;Foucusing on Circular Economy
Fundamental Research for
Producing High-Purity & High-Cleanliness Stainless Steels
(고순도/고청정 스테인리스강 제조기술 개발을 위한 열역학적 연구)
Influence of Refractory-Steel Interfacial Reaction
on the Formation Behavior of Inclusion in Ce-containing Stainless Steel Melt
(Kwon and Park; ISIJ Int., 2015, vol.55, p.2589-2596) ; Sawamura Awarded Paper [link]
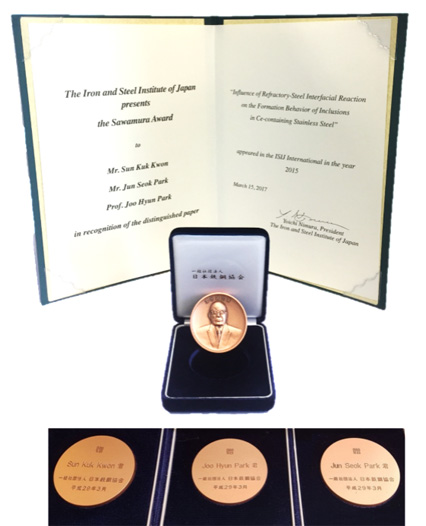
Microalloying of weld metal with Ce has also been shown to significantly improve weldability and oxidation resistance of ASS with grain refinement, decreased dendrite arm spacing and lower hot cracking property due to enhanced oxide scale adherence. The Ce-bearing ASS has been reported to show excellent antibacterial property compared to conventional Cu-bearing ASS when the amount of Ce added is above a critical value, e.g. 0.01 to 0.1 wt%, which is attributed to the Ce-rich zone precipitated in steel matrix.
Even though the bulk steel chemistry is possibly affected by the steel-refractory interfacial reactions for the systems containing highly reactive elements such as REE, there are few reports on this topic. Therefore, in the present study, we examined the thermodynamic effect of Ce addition on the interfacial reaction between alumina refractory and stainless molten steel at 1873 K, which contributes to the changes in steel chemistry and thus inclusion evolution process.
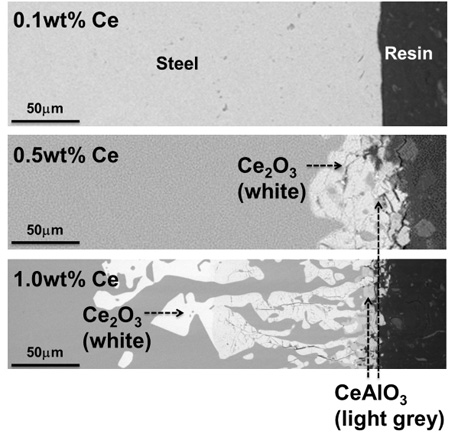
Backscattered electron image for the reaction products at the steel side in equilibrium with alumina refractory. refractory.
Effect of Al deoxidation on the formation behavior of inclusions in Ce-added stainless steel melt
(Kwon and Park; Met. Mater. Int., 2014, vol.20, p.959-966)
Austenitic stainless steels (ASS) are the most widely used structural materials in applications which require both high strength and excellent corrosion resistance in an aggressive environment. However, they are not immune to localized corrosion. Rare earth elements (REE) like Ce have been reported to form a thermodynamically stable surface film composed of CeOx, which improves the resistance to pitting, crevices, and intergranular (stress) corrosion.
The total oxygen content in Ce added stainless steel melts is strongly dependent on the composition of inclusions. That is, the higher the content of Ce2O3, the greater the density of inclusions, which results in a higher total oxygen content. However, some researchers reported that Ce addition enhanced the removal of oxygen. Moreover, the shape of Ce oxide inclusions, e.g. single particles or clusters, affects the cleanliness of steel melts. Therefore, in the present study, we examined the effect of Al deoxidation on the oxygen content as well as on the inclusion properties (composition, size and morphology) of Ce-added stainless steel melts at 1873 K.
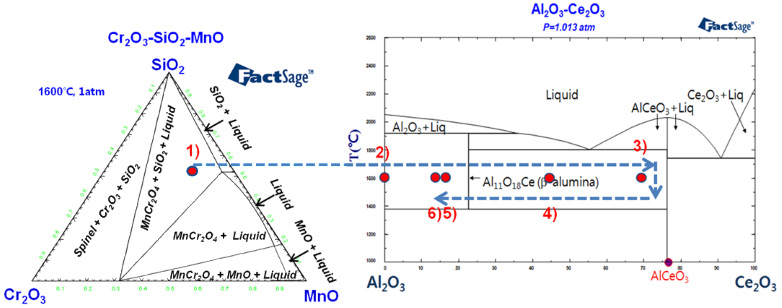
Trajectory of inclusion composition in the Al/Ce-added 25% Cr-20% Ni-1% Si-1% Mn steel at 1873 K.
Control of MgO.Al2O3 Spinel Inclusions in Stainless Steels – A Review
(Park and Todoroki; ISIJ Int., 2010, vol.50, p. 1333)
The demand of improved steel quality has been increasing year by year in terms of various view points such as strength, toughness, elongation, fatigue property, corrosion resistance, cleanliness, surface finishing and so on. It can be recognized that, among the requirements stated above, improvement in cleanliness, mentioned in this review, has been recently progressed considerably. Steelmakers have been always making great efforts to produce clean steels minimizing population of inclusions by decreasing oxygen content. It is generally known, however, that inclusion compositions strongly depend on the variation of oxygen content in conjunction with slag chemistry. The control of inclusion compositions, in which behaviour of alumina inclusions was dominated, was significantly advanced in the field of refining carbon steels.
This review summarizes the latest publications regarding the development of technology to control inclusion compositions focusing on MgO.Al2O3 spinel inclusions. The progress in research as for this topic made in universities and steel industries is worth documented particularly during the last two decades. This review aims at demonstrating what have been carried out to solve problems taking the following matters into account. To begin with the problems caused by spinel inclusions, which affect practice as well as for products, some examples of defects and clogged immersion nozzles for CC (continuous casting machine) are shown. The formation mechanism of MgO.Al2O3 spinel inclusions is secondly explained thermodynamically from the view points of chemistries of molten steels and slag compositions. Most recent progress of the basic studies is summarised which provide thermodynamic data of standard free energy changes of the reactions relating to MgO.Al2O3 spinel formation. As well, the interaction coefficients recently measured are shown that enable to obtain activities of dissolved elements that compose spinel. To predict the formation, activities of oxides in relation to spinel formation are also so important that the data related are shown. Furthermore crystallization behaviour of spinel is introduced. Countermeasures conducted in practice are shown along with some problems still left that should be solved in the future.
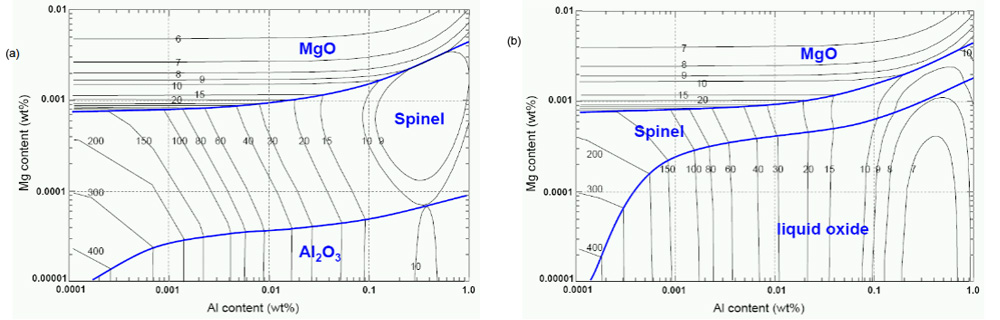
Phase stability diagram of inclusions with iso-oxygen contours in 18wt%Cr-8wt%Ni (a) and 18wt%Cr-8wt%Ni-2ppmCa steels (b) at 1873 K. Calculated
by FactSageTM6.1.
by FactSageTM6.1.
Thermodynamics of the Formation of MgO-Al2O3-TiOx Inclusions in Ti-stabilized 11Cr Ferritic Stainless Steel
(Park, Lee and Gaye; Metall. Mater. Trans. B, 2008, vol.39B, p.853)
Titanium stabilized ferritic stainless steels have been the subject of previous studies related to clogging of the submerged entry nozzle (SEN) during continuous casting process and control of the solidification structure through heterogeneous nucleation by the inclusions containing Ti oxide or nitride. In view of productivity of the melt shops and surface quality (sliver, flaw or crack) of steel products, it is desirable to have the amount of inclusions as low as possible. On the contrary, the use of inclusions is expected to help produce fine grains during primary solidification, which is preferable to other methodologies such as controlled deformation and heat treatment. In these studies, the MgAl2O4 spinel inclusion could accelerate the formation of TiN in molten steel due to very low disregistry between them and finally an equiaxed fine-grained structure was produced by the heterogeneous nucleation of delta ferrites on the TiN particles.
Clogging phenomena of SEN or tundish nozzle during continuous casting of Ti-stabilized stainless steels have been investigated by several researchers. Even though these studies described well the phenomena of the clogging and inclusions in the stainless steel industry, thermodynamic understanding for the effect of slag composition on the complex oxides in Ti-stabilized ferritic stainless steel is still insufficient. In-depth thermodynamic and kinetic studies on the effect of slag on the formation mechanism of spinel inclusions in Ti-free 16%Cr ferritic stainless steel have been investigated by Park and Kim. In this study, the composition of the inclusion was strongly affected by that of top slag. For example, the more basic slag (CaO or MgO saturation) equilibrated with the molten steel, the more MgO-rich spinel inclusions were observed.
Therefore, in the present study, based on the preceding view of thermodynamic and kinetic studies, the equilibration between CaO-SiO2-MgO-Al2O3-CaF2 (-TiO2) slag and Ti-stabilized Fe-11%Cr ferritic stainless steel melts has been investigated at 1873 K in order to clarify the effect of Al and Ti addition as well as that of slag composition on the formation of complex oxide inclusions containing Ti.
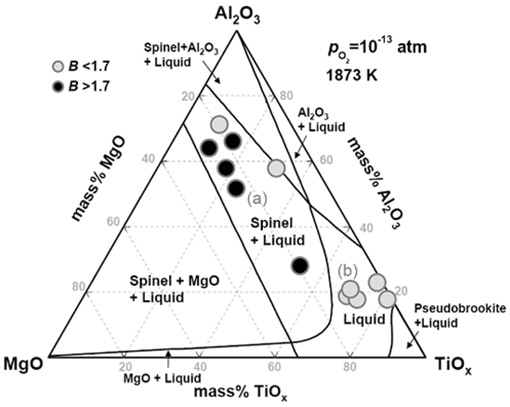
Computed phase diagram of MgO-Al2O3-TiOx system at 1873 K and pO2 = 10-13 atm. Circles are the average composition of ten inclusions per sample.
Thermodynamic Investigation on the Formation of Inclusions containing MgAl2O4 Spinel during 16Cr-14Ni Austenitic Stainless Steel Manufacturing Processes
(Park; Mater. Sci. Eng. A, 2008, vol.472, p.43)
The oxide inclusions, especially hard aluminates, have been known to be harmful to the mechanical properties of the steel welds as well as the steel material itself. The tensile deformation behavior of the notched 18%Cr-10%Ni austenitic stainless steel was dependent on the inclusion decohesion. Non-metallic inclusions containing aluminates were detrimental to the initiation of the corrosion-fatigue cracks in the 23%Cr-11%Ni stainless steels. The magnesium aluminate (MgAl2O4, spinel) inclusions have been known to be deleterious not only to the surface brightness but also to the press formability of the stainless steel products. These spinel particles have been originated from the inclusions at continuous cast slabs. The spinel phase could be crystallized in the calcium aluminosilicate inclusion matrix during transfer of molten steel from an argon oxygen decarburization (AOD) converter to the continuous casting (CC) machine, viz. tundish to mold, in the conventional stainless steelmaking processes. Hence, some industrial researchers have investigated the formation behavior of spinel inclusions based on the laboratory experiments or plant trials.
The systematic approach to the solidification behavior of the CaO-SiO2-MgO-Al2O3(-F) systems and the effect of 'F' content on the crystallization behavior of spinel during slow cooling cycles has recently been reported by Park. The computational phase equilibria and the microstructural analysis indicated that the Al2O3 or CaF2 affected the liquidus or solidus of the oxide inclusion systems, resulting in the changes of the nucleation and growth behavior of spinel crystals. Although these studies are meaningful to find the crystallization phenomena of the spinel phase in the liquid inclusions during the stainless steelmaking and casting processes, the thermodynamic equilibria between the steel melts and the inclusion compositions are not specifically investigated yet.
Therefore, in the present study, the fundamental thermodynamics for the relationship between the chemistries of the Fe-16%Cr-14%Ni austenitic stainless steel melts and the composition of the inclusions was investigated. Furthermore, the formation mechanism of the inclusions containing the spinel crystals has been developed based on the experimental results as well as the compositions of the inclusions in the steel samples taken during the plant operations.
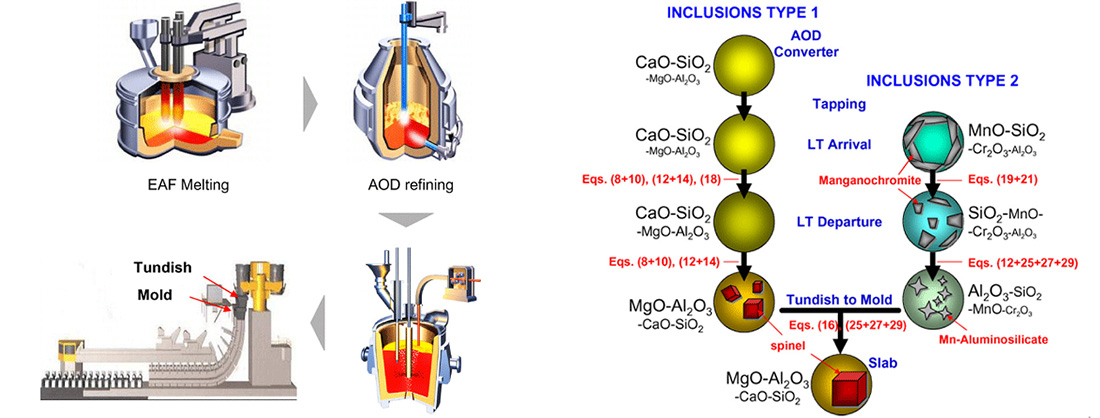
Conventional manufacturing processes of austenitic stainless steels.
Schematic illustration of the formation mechanism of the inclusions
containing spinel crystals during stainless steel manufacturing processes.
containing spinel crystals during stainless steel manufacturing processes.