Research
home
Fundamental Research for Producing High-Purity & High-Cleanliness Stainless Steels
Refining of High-Mn Steels for Generation Applications
Applications of Computational Thermodynamics for Producing High-Clean Steels ; Focusing on Smart Manufacturing
Novel Manufacturing Processes for Advanced High-Entropy Alloys
Grain Refinement of Macro-& Microstructure of Steels using Non-Metallic Inclusion
Zn-AI-Fe Dross Formation Mechanism in Hot Dip Galvanizing Bath for Producing Advanced Automotive Sreels
Physical Chemistry of MnO-base Slags for Producing High-Functional Manganese Ferroalloys
Viscosity-Structure Relationship of Molten Slags and Glasses
High Temperature Physical Chemistry of Metals and Slags
Characterization of Chemical Reactions at Slag-Refractory Interface in High Temperature Reactors
Extraction and Purification of Titanium and Its Alloys
Physical Chemistry of Molten Salts for Producing Magnesium and Zirconium
Recovery of Precious- & Rare Metals from Electric Wastes and Industrial By-products ;Foucusing on Circular Economy
Applications of Computational Thermodynamics
for Producing High-Clean Steels ; Focusing on Smart Manufacturing
(고청정강 제조를 위한 컴퓨터 시뮬레이션 응용 ; 스마트 제조공정의 구현)
Effect of Physicochemical Properties of Slag on the Removal Rate of Alumina Inclusions in the Ruhrstahl-Heraeus (RH) Refining Conditions
(Kim, Yang and Park; Metall. Mater. Trans. B, 2022, vol. 53B, pp. 2523-2533)
It is well known that the alumina-rich non-metallic inclusions, which are spontaneously formed by aluminum deoxidation of molten steel during the steelmaking processes, cause both the deterioration of the mechanical properties and severe problems during continuous casting processes. Therefore, it is necessary to remove the alumina-rich inclusions using top slags during the secondary refining processes, for example, Ruhrstahl–Heraeus (RH) reactor. The removal of inclusions from molten steel to slag is conducted according to the following consecutive processes: (i) flotation of inclusions to the steel–slag interface, (ii) separation of inclusions across the steel–slag interface by overcoming interfacial tension, and (iii) dissolution of inclusions into the slag phase. The dissolution of the alumina inclusions is the rate controlling process in terms of removal of alumina-rich inclusions during the secondary refining processes.
In the present study, we have investigated the relationship between the physicochemical properties and the inclusion removal ability of the CaO–Al2O3–FetO–SiO2–MgO (RH-type) slag by accounting for the interfacial reaction between molten steel and slags. Furthermore, computational simulations were developed to predict the oxygen behavior in molten steel under condition of commercial RH operation, which was determined using inclusion removal rate in the steel and slag–metal reaction kinetics.
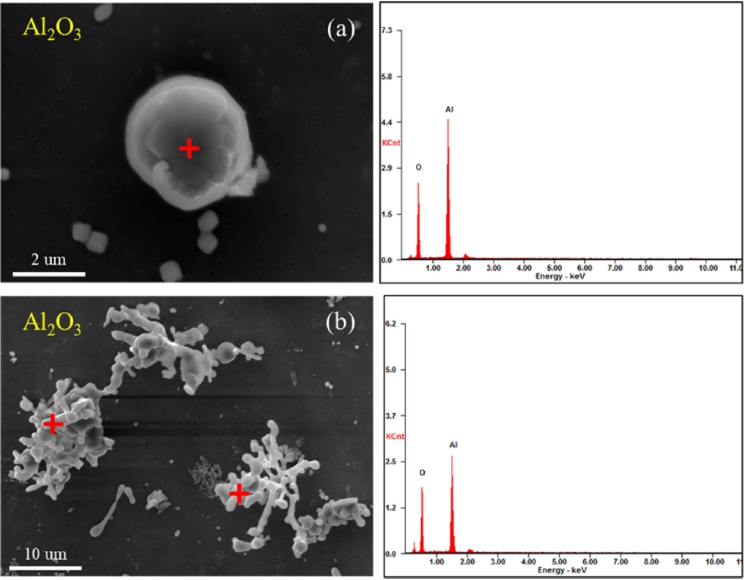
Three-dimensional morphologies of the alumina inclusions within 30 s after aluminum addition to the steel: (a) spherical single and (b) aggregated alumina inclusions
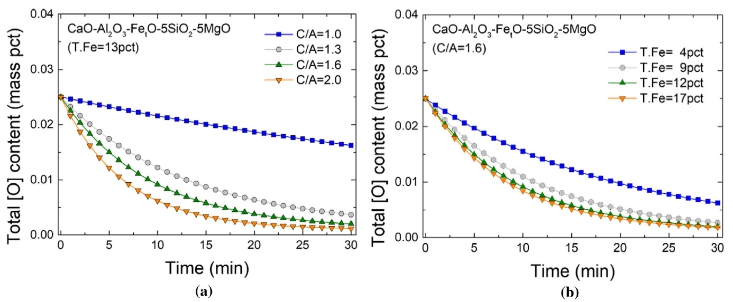
Computational results of total oxygen in the steel
with (a) C/A ratios at fixed iron content and (b) iron content at fixed C/A ratios
in the slags in the RH process.
with (a) C/A ratios at fixed iron content and (b) iron content at fixed C/A ratios
in the slags in the RH process.
Influence of calcium aluminate flux on reoxidation behaviour of molten steel during continuous casting process
(Kim, Holappa and Park; Ironmaking & Steelmaking, 2020, vol.47, pp.84-92)
Because the continuous casting tundish is the last metallurgical reactor for removing non-metallic inclusions before distributing molten steel into casting strands, it is essential to control reoxidation of molten steel in the tundish for manufacturing high cleanliness steel products. The entrapment of carryover ladle slag, reaction with tundish flux, degradation of the refractory, reaction with ladle well packing materials, and/or oxidation by air contaminate molten steel in the tundish.
Consequently, the effect of calcium aluminate-based tundish flux (CA-flux) on the reoxidation behaviour of molten steel was investigated by employing computational simulations based on the ReSMI reaction model to predict inclusion evolution. The simulation was adopted to predict the reoxidation of molten steel in tundish during a continuous casting process.
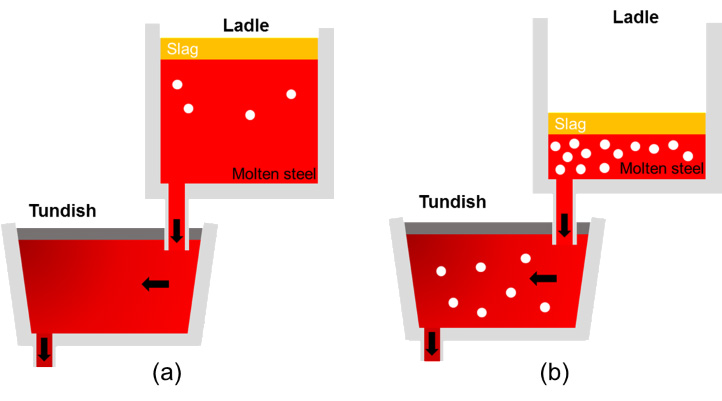
Schematic of the (a) initial and (b) last stage in the continuous casting process.
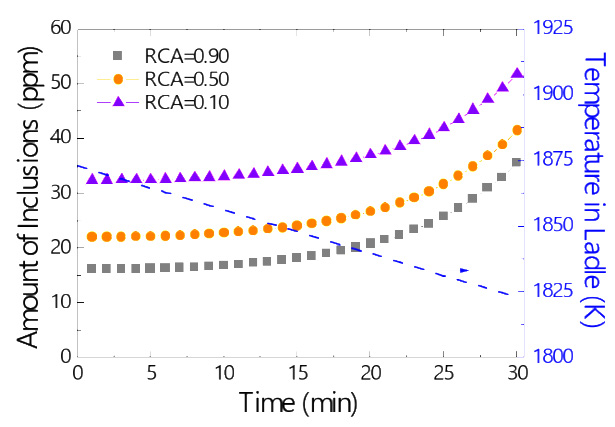
Variation in the number of inclusions in the molten steel at the end of tundish process and the temperature of the molten steel in the ladle as a function of casting time during continuous casting.
Effect of CaO/Al2O3 ratio of ladle slag on formation behavior of inclusions in Mn and V alloyed steel
(Shin and Park; ISIJ Int., 2018, vol.58, pp.88-97)
The Mn and V alloyed steel, which has a ferrite-pearlite composite microstructure, have been widely used as automotive parts such as crankshafts, push rods, rotating bearings, etc. due to its excellent machinability and high-strength. However, the product performance can be significantly affected by the steel cleanliness. Gojić et al. reported the resistance to hydrogen embrittlement could be improved by lowering the non-metallic inclusions. In addition, the MgAl2O4 spinel inclusion, which generally formed during the ladle refining process, potentially causes nozzle clogging as well as surface defects in products. Hence, it is crucial to predict and control the inclusion composition during the ladle refining process.
In the present study, therefore, the multiphase reactions among the Mn and V alloyed steel melt, the CaO–Al2O3–SiO2–MgO–CaF2 slag and the MgO refractory were investigated to understand the evolution mechanism of the inclusions using both high temperature experiments and ReSMI multiphase reactions simulation. The CaO/Al2O3 (=C/A) ratio of the ladle slag was varied to understand the effect of slag basicity on the formation behavior of inclusions. Moreover, the optimum range of slag basicity to suppress the harmful spinel inclusion will be proposed.
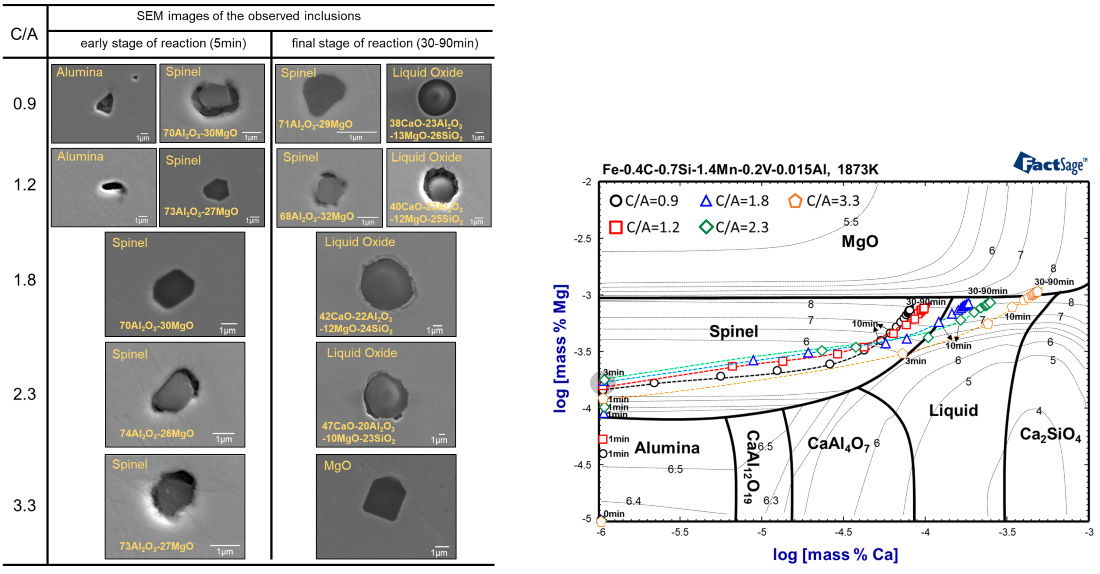
SEM images of the typical observed inclusions at early (5-min) and final (90-min) stage of the reaction.
Phase stability diagram of inclusions with iso-oxygen contours in the Fe-0.4C-0.7Si-1.4Mn-0.2V-0.015Al melt containing Mg and Ca at 1873 K. Calculated by FactSage7.1.
Modification of Inclusions in Molten Steel by Mg-Ca Transfer from Top Slag: Experimental Confirmation of the 'Refractory-Slag-Metal-Inclusion (ReSMI)' Multiphase Reaction Model
(Shin and Park; Metall. Mater. Trans. B, 2017, vol.48B, pp.2820-2825)
High clean steels have been widely employed in automotive parts. However, the product performance can be significantly affected by the steel cleanliness. Alumina and MgAl2O4 spinel inclusions, which are formed during the ladle refining process, have the potential to cause nozzle clogging and defects in products. Hence, it is crucial to predict and control the inclusion composition during the ladle refining process. The thermodynamics of the formation behavior and modification of spinel inclusions in molten steel have been investigated since the 1980s. Specifically, Park et al. reported the formation mechanisms of spinel inclusions and suggested countermeasures for use during stainless steel refining and casting. Todoroki and Mizno reported that silica in the slag inhibited the modification of spinel inclusion to liquid oxide inclusion by suppressing the extensive reduction of CaO in the slag.
Therefore, we investigated the effect of ladle slag composition on the formation behavior of non-metallic inclusions during the ladle refining process using both experiments and ReSMI multiphase reaction simulations in the present study. Our overall objective was to confirm that spinel inclusions could be converted to liquid inclusions by slag-metal reactions without direct calcium addition during the ladle refining process.
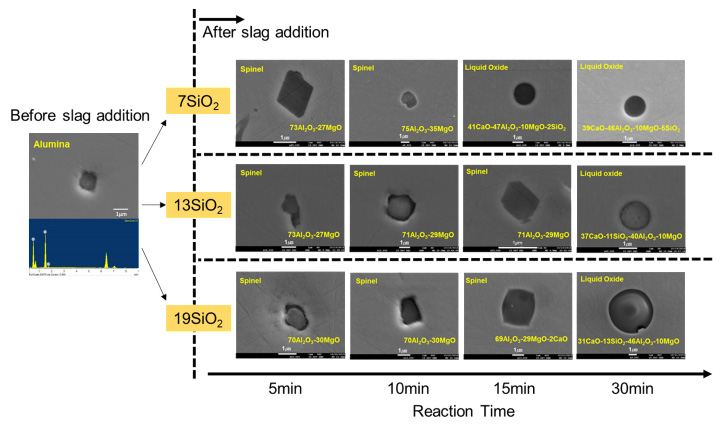
SEM images of a typical observed inclusion at 1873 K. Numbers represents mass pct of each oxide.
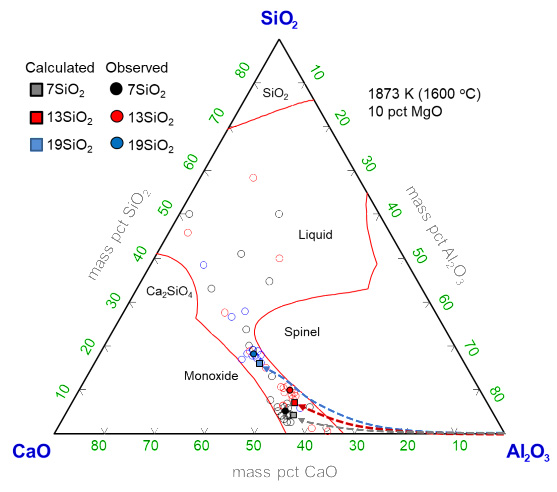
Trajectory of the calculated composition of the inclusions and average composition of measured inclusion in molten steel reacted with ladle slag at 1873 K.
Refractory-Slag-Metal-Inclusion Multiphase Reactions Modeling using Computational Thermodynamics: Kinetic Model for Prediction of Inclusion Evolution in Molten Steel
(Shin, Chung and Park; Metall. Mater. Trans. B, 2017, vol.48B, pp.46-59)
Performance of steel products is significantly affected by the steel cleanliness. Especially, the MgAl2O4 spinel inclusion is very harmful because it causes the nozzle clogging as well as the surface defects in semi and final products. Hence, it is crucial to avoid the formation of spinel during the secondary refining process. The spinel inclusion is formed by the complicated slag–metal–refractory multiphase reactions during ladle refining process. Therefore, it is important to understand the complex multiphase reactions for controlling the spinel formation behavior.
Therefore, in order to predict the evolution of inclusions during the ladle refining process, the refractory–slag–metal–inclusion multiphase reaction model was developed by integrating the refractory–slag, slag–metal, and metal–inclusion elementary reactions. For the convenient and flexible extendibility of the present refractory–slag–metal–inclusion multiphase reaction model, only the effective reaction volume in the metal and slag phase, and the mass transfer coefficient of MgO in the slag were employed in the model. These values were directly measured in the present study. Finally, the effect of slag composition on the evolution process of inclusions was simulated using the refractory–slag–metal–inclusion multiphase reaction model developed in the present study.
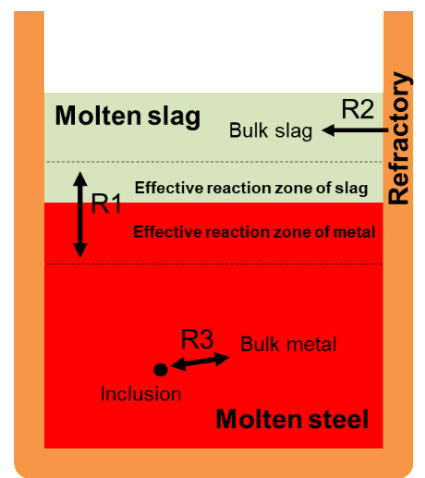
Schematic representation of the slag-metal (R1), refractory-slag (R2), and inclusion-metal (R3) reactions in the present multiphase modeling system.
Effect of Slag Composition on the Concentration of Al2O3 in the Inclusions in Si-Mn-killed Steel
(Park et al.; Metall. Mater. Trans. B, 2014, vol.45B, pp.953-960)
Non-metallic inclusions in steel cause deterioration of mechanical properties as well as severe problems during steel processing. The cleanliness of the steel is important in spring steel and tire cord steel since nonmetallic inclusions act as crack initiation sites when subjected to cyclic stress. However, no steel can be totally free from inclusions. For this reason, Si and Mn are generally used as deoxidizers in spring steel and tire cord steel in order to avoid harmful Al2O3-rich inclusions. A number of studies have been carried out to identify techniques that achieve inclusions that are as harmless as possible. The application of optimized slag to suppress the formation of harmful inclusions such as alumina and spinel is one such method used for various steel grades including Si-Mn-killed steel.
Therefore, in the present study, the equilibria between CaO-Al2O3-SiO2-CaF2-MgO(-MnO) slag and Fe-1.5 mass pct Mn-0.5 mass pct Si-0.5 mass pct Cr melt was investigated at 1873 K in order to understand the effect of slag composition on the concentration of Al2O3 in the inclusions.
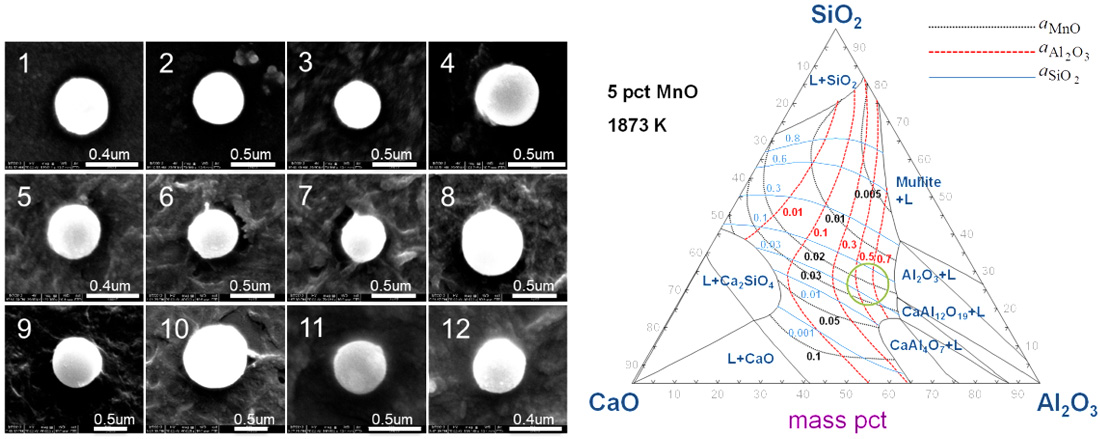
The morphology of inclusions observed in each sample by SEM.
Iso-activity contours of MnO, Al2O3, and SiO2 in the CaOSiO2-Al2O3-5 pct MnO slag at 1873 K. The circle is the recommended slag composition for obtaining liquid inclusion, liquidus temperature of which is lower than 1573 K in Si-Mn-killed steel refined in the alumina ladle.