Research
home
Fundamental Research for Producing High-Purity & High-Cleanliness Stainless Steels
Refining of High-Mn Steels for Generation Applications
Applications of Computational Thermodynamics for Producing High-Clean Steels ; Focusing on Smart Manufacturing
Novel Manufacturing Processes for Advanced High-Entropy Alloys
Grain Refinement of Macro-& Microstructure of Steels using Non-Metallic Inclusion
Zn-AI-Fe Dross Formation Mechanism in Hot Dip Galvanizing Bath for Producing Advanced Automotive Sreels
Physical Chemistry of MnO-base Slags for Producing High-Functional Manganese Ferroalloys
Viscosity-Structure Relationship of Molten Slags and Glasses
High Temperature Physical Chemistry of Metals and Slags
Characterization of Chemical Reactions at Slag-Refractory Interface in High Temperature Reactors
Extraction and Purification of Titanium and Its Alloys
Physical Chemistry of Molten Salts for Producing Magnesium and Zirconium
Recovery of Precious- & Rare Metals from Electric Wastes and Industrial By-products ;Foucusing on Circular Economy
Extraction and Purification of Titanium and Its Alloys
(생체/항공재료용 Ti의 제련 및 정련기술 (collaboration with
Dr. HS Park, KIGAM, Prof. DJ Min, Yonsei University and Dr. BM Moon, KITECH))
Improving the production efficiency of high-titania slag in Ti extraction process: fluxing effect on formation of pseudobrookite
(Kim, Heo and Park; Scientific Reports, 2020, vol.10, article number 6530, pp.1-12)
As titanium has good physical and chemical properties, e.g. excellent strength, corrosion resistance, fatigue resistance, fracture toughness, and high-temperature characteristics, its demand steadily increases. The major raw material for titanium extraction is rutile (~95% TiO2), which quickly is being depleted. Therefore, ilmenite (FeTiO3, 30–65% TiO2) as a substitutional resource is in the spotlight. There are previous studies about the ilmenite smelting process in conjunction with pre-oxidation treatment, which improves the reactivity of ilmenite. After the pre-oxidation treatment, the ilmenite ore is sent to direct leaching or high temperature reduction stages according to the consecutive processes.
Most of the previous studies have been conducted at temperatures up to 1673 K, which is relatively lower than the ilmenite smelting temperature. Moreover, there have been no investigations of fluxing effect under ilmenite smelting conditions. Therefore, in the current study, we attempted to maximize the reduction of FeO from ilmenite by controlling the physicochemical factors affecting the reduction kinetics with fluxing method.
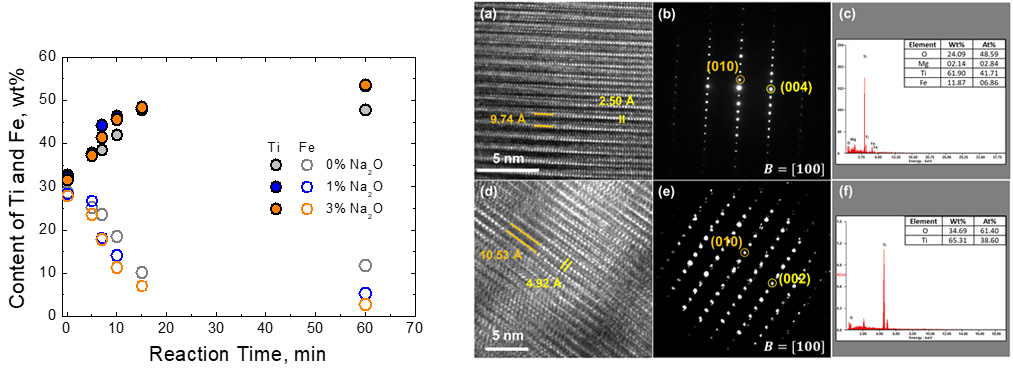
Variation of titanium and iron content in slags for Na2O fluxing experiments as a function of reaction time at 1873 K.
(a) High resolution (HR) image, (b) diffraction pattern (DP) and (c) EDS spectrum of ps-BR phase in untreated slag sample, and (d) HR image, (e) DP of and (f) EDS spectrum of ps-BR phase in Na2O-fluxed slag sample.
Influence of temperature on reaction mechanism of ilmenite ore smelting for titanium production
(Kim, Heo and Park; Metall. Mater. Trans. B, 2019, vol.50B, pp.1830-1840)
Titanium has good physical and chemical properties, such as excellent strength, corrosion resistance, fatigue resistance, fracture toughness, and high-temperature characteristics. Therefore, it is expected that there will be steady demand for titanium in the fields of desalination, power generation, etc. To obtain high yields of titanium, relatively high-concentration TiO2, such as rutile (~ 95 mass pct), should be used as a raw material. However, rutile is a limited resource in nature. Alternatively, ilmenite is regarded as a promising resource. According to a U.S. geological survey, there are 62 million tons of rutile reserves in the world and 870 million ton of ilmenite reserves. Therefore, ilmenite ore, which is more than ten times as abundant as rutile, has become an important source for producing titanium.
Several researchers have investigated the solidification of the M3O5 phase as a result of the reduction of FeO in ilmenite, as well as the role of impurities (e.g., SiO2, CaO, and MgO). However, few studies have conducted the reaction mechanism based on kinetic analysis of the smelting reduction as a function of temperature. Hence, in the present study, the carbothermic smelting reduction process of ilmenite ore at high temperatures was simulated by thermodynamic computations using FactSage7.0; the experimental conditions were designed based on these findings. We then conducted high-temperature experiments using an induction furnace by employing in-situ sampling and quenching methodology.
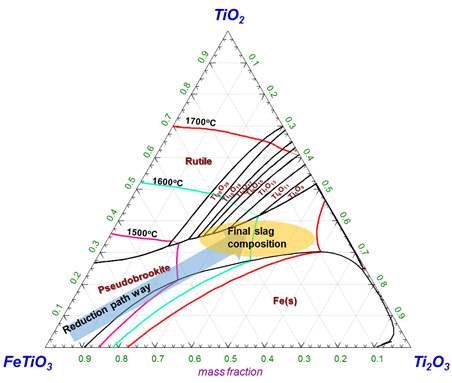
Reaction path of smelting process plotted on the TiO2-Ti2O3-FeTiO3 ternary phase diagram.
Method of recycling titanium scrap via the electromagnetic cold crucible technique coupled with calcium treatment
(Moon, Seo, Lee, Jung and Park; J. Alloys & Compd., 2017, vol.727, pp.931-939)
Titanium, the ninth-most abundant element in the Earth's crust, has been used in the aerospace industry since 1948. Since then, Ti and its alloys have been widely used in various applications such as in ships, chemical plants, automobiles, and even medical implants. They possess several attractive properties as structural materials for use in modern industries, including low density, high specific strength, good corrosion resistance, and high workability. Hence, many researchers and engineers have investigated the processing of Ti and its resulting microstructures and properties. However, the production of Ti still faces numerous challenges. The global production volume of Ti is substantially lower than those of Fe and Al. The cost of processing a thousand cubic feet of Ti, which includes melting and refining, is five times higher than that of Al. In particular, the cost of processing Ti ingots, which includes fabricating plates, billets, and rods by rolling or forging, is ten times higher than that of Al. In addition, the poor forming ability of Ti leads to large amounts of Ti wastes and a low rate of material usage. Therefore, the development of methods for recycling Ti wastes such as Ti scraps is a topic worth researching. Ti scraps are inevitable in the processing of final product shapes from mill products during machining. Contamination by oxygen during processing and cutting is also unavoidable. Owing to Ti's high affinity toward oxygen, a large amount of interstitial oxygen exists in Ti scraps and degrades the mechanical and physical properties such as ductility, fracture toughness, and corrosion resistance.
Thus, the present study focuses on recycling Ti scrap via the electromagnetic cold crucible (EMCC) process coupled with Ca treatment. An EMCC process, which comprises an electromagnetic cold crucible with a feeder system, is a promising method for melting Ti scraps and producing high-purity Ti continuously and productively. Ti scraps are melted in a water-cooled copper crucible, and various amounts of Ca are added to the molten Ti. The composition of the refined Ti ingot is characterized by elemental analysis and inductively coupled plasma-optical emission spectroscopy (ICP-OES). The microstructure of the refined Ti ingot is investigated via optical microscopy and field emission-scanning electron microscopy (FE-SEM). The mechanical properties are examined using hardness and tensile strength tests.
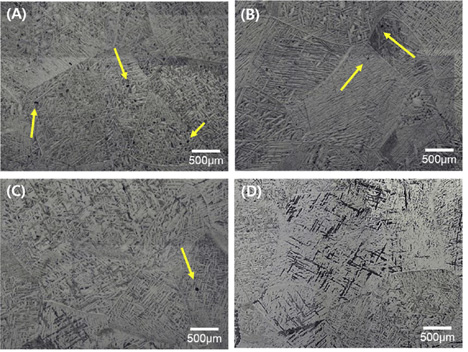
Typical microstructures of (A) as-melted Ti and Ti after Ca treatment with (B) 0.1% Ca, (C) 0.3% Ca, and (D) 0.5% Ca.
Diffusion of Oxygen in Beta-Titanium
(Song, Han, Min, Choi, and Park; Scripta Mater., 2008, vol.59, p.623)
Titanium is an attractive material with excellent corrosion resistance and high strength-to-weight ratio. Industrial applications of Ti have expanded in many areas such as the aerospace, marine, chemical plants and even automobiles. The effect of interstitial solutes such as O or N in Ti is of considerable importance as a result of the marked effect of these elements on the mechanical properties such as ductility and fracture toughness. Especially, knowledge about the diffusion rate of O in Ti can be applied to the evaluation of the extent of contamination in high-temperature creep deformation or oxidation of Ti and its alloys.
However, they are scattered over a period of more than 50 years, which could be originated from the different experimental techniques and the amount of impurities in each study. Many of these studies employed the gaseous oxidation method, which generates not only the oxide scale but also an O concentration gradient in Ti substrate. The gaseous oxidation method, however, cannot thoroughly exclude the effect of several Ti oxides such as TiO and Ti2O3. Furthermore, the diffusion coefficients can be strongly dependent on the concentration, whereas few systematic investigations have been performed on the effect of O concentration.
The present work is concerned with the measurement of O diffusivity in beta-Ti as a function of temperature and concentration by the molten flux method. We can determine the direction of oxygen transfer by the composition of the molten fluxes. For example, O atoms will diffuse out from bulk Ti to the Ti/flux interface when the strongly reducing fluxes such as the Ca-CaCl2 system are reacted, while the O will diffuse into the bulk Ti from the interface when the oxidizing fluxes such as the CaO-CaCl2 system are used. The oxygen potential, viz. the driving force of O transfer at Ti/flux interface, can be determined by the thermodynamic activity of Ca or CaO in the fluxes, which is well described in the literature.
The advantages of the molten flux method are also that the formation of TiOx layer at the interface can be prevented due to strong affinity of Ca with O than that of Ti with O based on the Gibbs free energy of the formation of each oxide. Finally, Ca and Ti do not form any intermetallic compound and the solubility of Ca in beta-Ti (BCC) is about 60 ppm at 1273 K. In the present study, the commercial pure (CP) Ti (0.055%C-0.14%Fe-0.32%O-0.006%N) was equilibrated with the CaO-CaCl2 flux at 1273 through 1473 K.
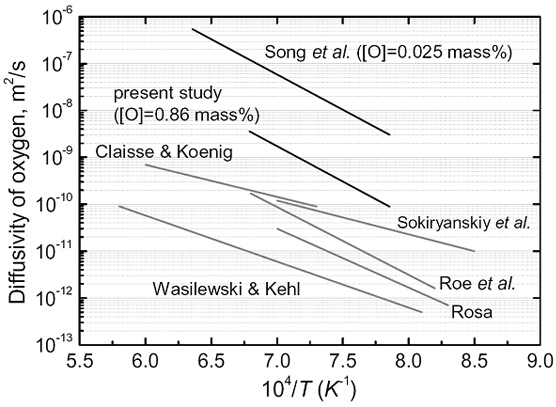
Comparison of the present and previous Arrhenius plots for O diffusion in beta-Ti.