Research
home
Fundamental Research for Producing High-Purity & High-Cleanliness Stainless Steels
Refining of High-Mn Steels for Generation Applications
Applications of Computational Thermodynamics for Producing High-Clean Steels ; Focusing on Smart Manufacturing
Novel Manufacturing Processes for Advanced High-Entropy Alloys
Grain Refinement of Macro-& Microstructure of Steels using Non-Metallic Inclusion
Zn-AI-Fe Dross Formation Mechanism in Hot Dip Galvanizing Bath for Producing Advanced Automotive Sreels
Physical Chemistry of MnO-base Slags for Producing High-Functional Manganese Ferroalloys
Viscosity-Structure Relationship of Molten Slags and Glasses
High Temperature Physical Chemistry of Metals and Slags
Characterization of Chemical Reactions at Slag-Refractory Interface in High Temperature Reactors
Extraction and Purification of Titanium and Its Alloys
Physical Chemistry of Molten Salts for Producing Magnesium and Zirconium
Recovery of Precious- & Rare Metals from Electric Wastes and Industrial By-products ;Foucusing on Circular Economy
Physical Chemistry of Molten Salts for Producing Magnesium and Zirconium
(에너지 소재용 Zr, Mg 제련 프로세스 개선을 위한 물리화학적 연구)
Mechanism of MgO dissolution in MgF2-CaF2-MF (M=Li or Na) melts: Kinetic analysis via in-situ high temperature confocal scanning laser microscopy (HT-CSLM)
(Lee, Yang, Min and Park; Ceram. Int., 2019, vol.45, pp.20251-20257)
Among the various technologies for magnesium extraction, the solid oxide membrane (SOM) process is environmentally friendly, has lower energy consumption, and zero carbon dioxide emission. Through direct electrolysis of metal oxides, magnesium is produced at a cathode with pure oxygen gas as the byproduct. In a previous study, we identified a low temperature SOM (LT-SOM) process utilizing a ceria-based oxygenion-conducting membrane anode that had energy- and cost-saving effects.
As global greenhouse gas emissions become more serious, the metal extraction industry is striving to adopt the direct electrolytic reduction process using halide-based flux. However, only a few studies investigated the dissolution reaction of oxide particles into the halide flux system. There is no approach to interpret the dissolution behavior of MgO in the halide flux system in terms of the viscosity of flux. As a result, this study will demonstrate the dissolution reaction of MgO in fluoride-based molten flux with the in-situ HT-CSLM measurement. Additionally, the dissolution rate and mechanism will be elucidated based on approximations of diffusion around the particle.

Schematic view of (a) the HT-CSLM and (b) experimental set-up for dissolution experiments.
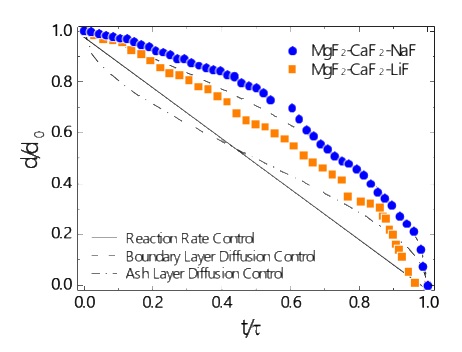
Normalized dissolution patterns of a MgO particle in MgF2-CaF2-LiF and MgF2-CaF2-NaF flux at 1473 K.
Thermodynamics of Fluoride-based Molten Fluxes for Extraction of Magnesium through Low Temperature Solid Oxide Membrane (LT-SOM) Process
(Lee, Yang and Park; Calphad, 2018, vol.62, pp.232-237)
There are various types of metallurgical processes for magnesium extraction, among which the Pidgeon process and the electrolysis process are commonly employed in the magnesium industry. In the Pidgeon process, dolomite is calcined to MgO and CaO, and these oxides are reduced by silicon to yield magnesium gas. In the magnesium chloride electrolysis process, molten magnesium is produced by chlorination of magnesium oxide. These methods have several disadvantages, including being energy intensive and having lower efficiency for the Pidgeon process and toxic gas emissions and thus environmental risks for the electrolysis process.
In addition, lowering the operating temperature below 1273 K would bring various advantages, including energy- and cost-saving effects. Correspondingly, ceria-based membranes have become of interest for anode assembly because of their superior ionic conductivity at lower temperatures (around 1273 K) compared to yttria-stabilized zirconia (YSZ) membrane. Therefore, in the present study, we investigated potential additives to introduce into the MgF2-CaF2 flux to lower the melting temperature, and we proposed a new flux system for the modified low temperature SOM (LT-SOM) process using a ceria-based membrane. Moreover, the solubility of MgO in fluoride-based molten fluxes was quantitatively evaluated based on thermodynamic calculations and experimental confirmation.
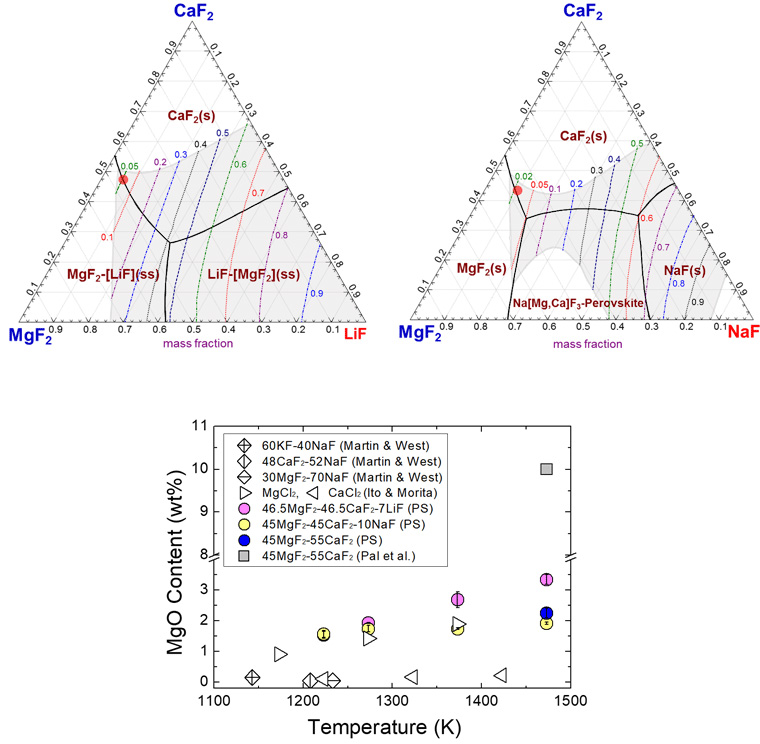
Liquidus projections calculated using ‘FTsalt’ database in FactSage™7.0 of MgF2-CaF2-LiF and MgF2-CaF2-NaF systems with isoactivity contours of LiF and NaF at 1223 K. The shaded regions represent the liquid phase at 1223 K.
Temperature dependence of MgO solubility in molten fluoride fluxes (PS; present study).
Effect of halide flux on physicochemical properties of MgCl2–based molten salts for accelerating zirconium production: Thermodynamic assessment
(Shin and Park; Metall. Mater. Trans. E, 2016, vol.3E, pp.218-226)
In the present process, the liquid magnesium reduces the gaseous zirconium tetrachloride, resulting in the production of metallic zirconium in the form of a porous mass (sponge) and liquid magnesium chloride (MgCl2). Temperature of 1073 K to 1173 K is maintained in the reaction chamber, called retort. In these conditions, the zirconium remains in the solid state in sponge form, and magnesium chloride and extra magnesium are in molten state.
In the present study, therefore, we tried to investigate the various halide flux systems includingMgCl2 not only for increasing the density of MgCl2-based molten salts but also for decreasing the activity of MgCl2 by employing the FactSageTM7.0 software, which is a commercial thermochemical computing package, in the viewpoint of the acceleration of the magnesiothermic reduction reaction of gaseous ZrCl4.
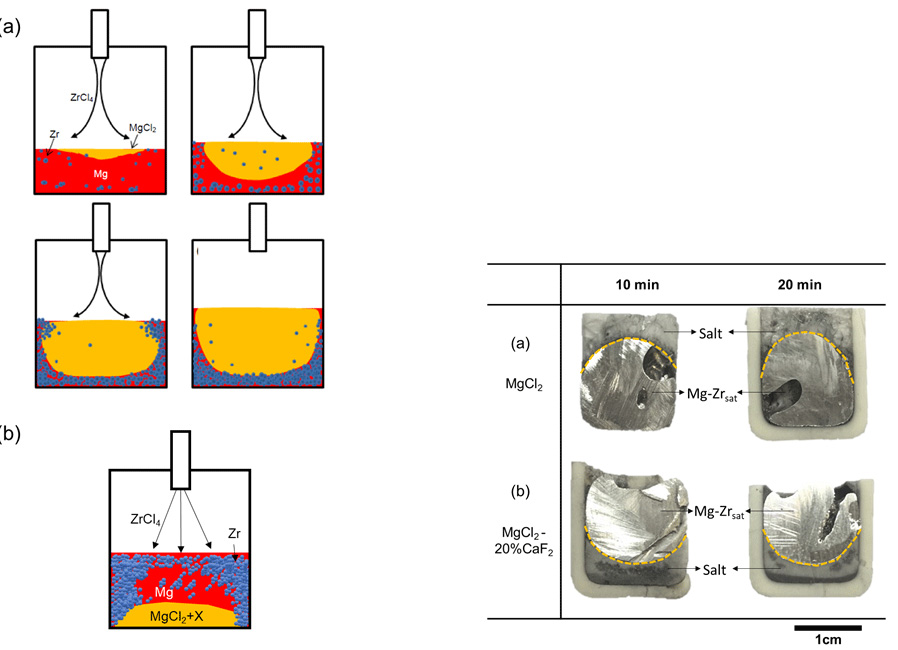
Schematic illustrations for (a) the general zirconium sponge formation mechanism reprinted with permission from Jang et al. and (b) the predicted mechanism under condition of increased density of MgCl2-based salt mixture.
The morphology of the cross section of the experimental samples of (a) MgCl2 melt and (b) MgCl2-20 pct CaF2.
Diffusion coefficient of gaseous zirconium tetrachloride (ZrCl4)
(Shin and Park; Fluid Phase Equilib., 2015, vol.389, pp.4-8)
In zirconium production, the raw material is zirconium tetrachloride (ZrCl4), which sublimates at about 603 K and melts at about 713 K (triple point). The rate of ZrCl4 sublimation may control the feed rate of reactants in a vessel in a way that affects production efficiency. According to Reshetnikov and Oblomeev, the overall processing rate is more influenced by the rate of ZrCl4 sublimation than the chemical reaction rate between ZrCl4 and liquid magnesium.
An experimental method for the measurement of the diffusion coefficient of organometallic compounds using thermogravimetric analysis (TGA) was reported by Siddiqi et al. This method has been very successful for the measurement of various diffusion coefficients. Thus, in the present study, we attempted to confirm the binary diffusion coefficient of ZrCl4 in an Ar gas atmosphere by using the TGA method.
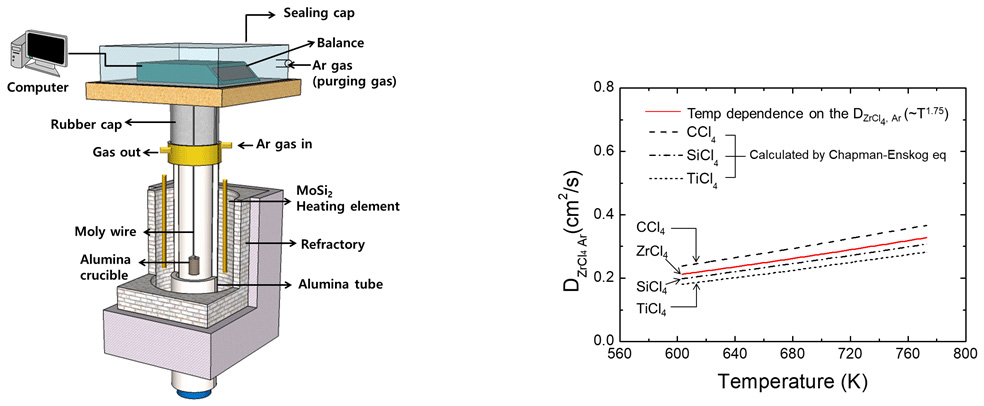
Schematic diagram of the experimental apparatus.
The 1.75 temperature power dependence of the diffusion coefficients on DZrCl4-Ar.
Isothermal and non-isothermal sublimation kinetics of zirconium tetrachloride (ZrCl4) for producing nuclear grade Zr
(Shin, Choi, Min and Park; Mater. Chem. Phys., 2014, vol.143, pp.1075-1081)
Zirconium and its alloy are used extensively as nuclear fuel cladding materials in water-cooled nuclear power reactors. However, only a few countries in the world have access to commercial-scale zirconium industries and have the capability to manufacture reactor-grade zirconium. Metallic zirconium (sponge) can be produced from a magnesiothermic reduction known as Kroll’s process, which is similar to that used for titanium production except that the raw material (TiCl4) is in the liquid state.
In the present study, we attempted to confirm the sublimation mechanism of ZrCl4 based on a kinetic study of its sublimation using thermogravimetic analysis (TGA). The activation energy of ZrCl4 sublimation was measured under both isothermal and nonisothermal conditions.
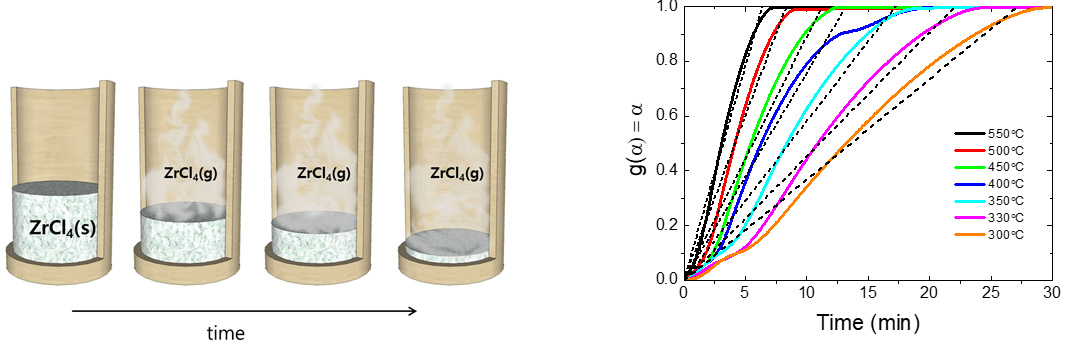
Schematic illustration of ZrCl4 sublimation.
g(a) vs. time under isothermal conditions at different temperatures.