Research
home
Fundamental Research for Producing High-Purity & High-Cleanliness Stainless Steels
Refining of High-Mn Steels for Generation Applications
Applications of Computational Thermodynamics for Producing High-Clean Steels ; Focusing on Smart Manufacturing
Novel Manufacturing Processes for Advanced High-Entropy Alloys
Grain Refinement of Macro-& Microstructure of Steels using Non-Metallic Inclusion
Zn-AI-Fe Dross Formation Mechanism in Hot Dip Galvanizing Bath for Producing Advanced Automotive Sreels
Physical Chemistry of MnO-base Slags for Producing High-Functional Manganese Ferroalloys
Viscosity-Structure Relationship of Molten Slags and Glasses
High Temperature Physical Chemistry of Metals and Slags
Characterization of Chemical Reactions at Slag-Refractory Interface in High Temperature Reactors
Extraction and Purification of Titanium and Its Alloys
Physical Chemistry of Molten Salts for Producing Magnesium and Zirconium
Recovery of Precious- & Rare Metals from Electric Wastes and Industrial By-products ;Foucusing on Circular Economy
Physical Chemistry of MnO-base Slags for Producing High Functional Manganese Ferroalloys
(고기능 Mn합금 정련기술 개발을 위한 MnO-계 슬래그의 물리화학적 특성 규명)
Effect of atmosphere and slag composition on the evolution of PH3 gas during cooling of reducing dephosphorization slags
(Shin and Park ; ISIJ Int., 2013, vol.53, pp.385-390)
High manganese steels (10 to 25 mass% Mn) are of interest due to their good mechanical properties including superior strength and good ductility. Accordingly, the demand for ultra-low phosphorous manganese alloys such as FeMn and SiMn alloys has recently increased. However, the conventional oxidizing dephosphorization technique is not applicable to manganese alloys because silicon or manganese will be oxidized before phosphorous under oxidizing conditions. Therefore, the dephosphorization should be carried out under a strongly reducing atmosphere to produce a low phosphorus manganese alloys. The mechanism of reducing dephosphorization using lime-based highly basic fluxes has been reported by several authors, and recently reviewed and experimentally confirmed by the present authors in previous study.
Therefore, this study consists of the distribution behavior of phosphorous between the CaO–CaF2 (–SiO2) flux and SiMn alloy melts at 1823 K, and includes the thermodynamic and kinetics analyses for the environmental stability of reducing refining slags under wet and dry cooling conditions based on the effect of slag composition on the evolution of PH3 gas.
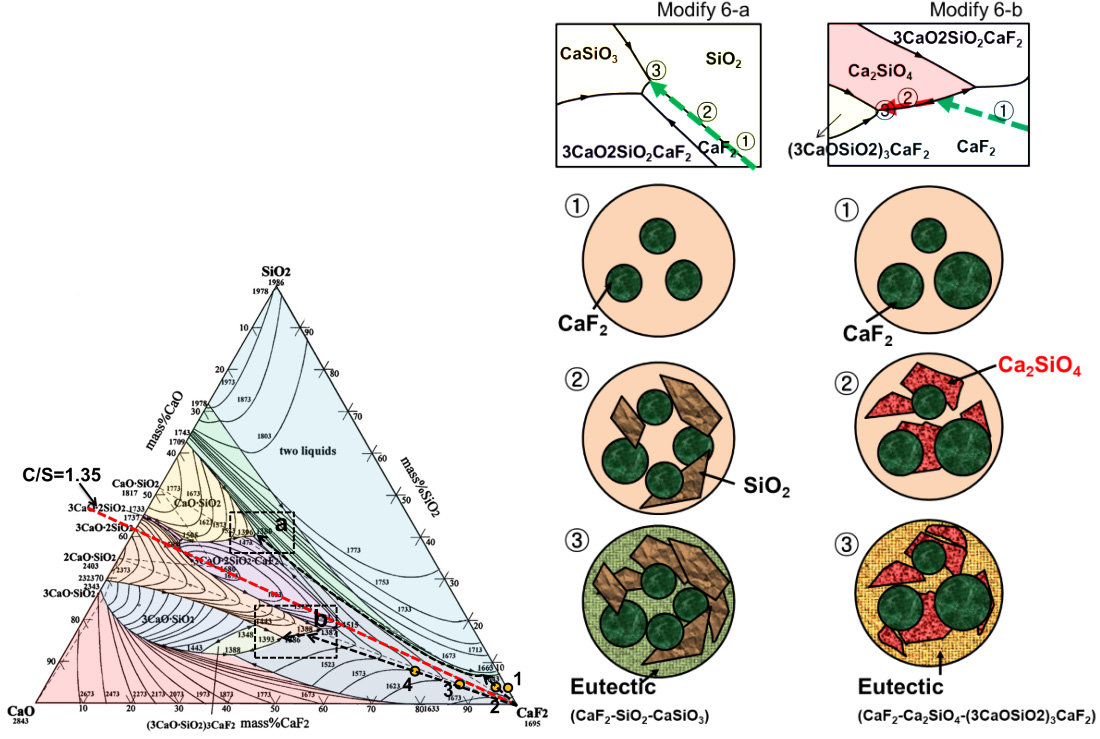
Slag composition after dephosphorization reaction plotted on the CaO–CaF2–SiO2 ternary phase diagram.
Schematic diagram of cooling path and solidification structure of dephosphorization slags.
In Situ Observation of the Dissolution Phenomena of SiC Particle in CaO-SiO2-MnO Slag
(Park et al.; J. Eur. Ceram. Soc., 2010, vol.30, p.3181)
A flexible electric furnace operation has widely been used in production of manganese ferroalloys such as high carbon ferromanganese (HC FeMn) and silicomanganese (SiMn), according to requirement. There are two operational strategies referred to as the discard slag practice (or basic slag operation) and the high MnO practice (or fluxless operation). In the latter, the MnO-rich slag is reprocessed for production of SiMn in duplex processing. In this way, the MnO content of the discard slag can be reduced to 5~10% MnO. There has been a shift in demand in many countries away from the use of HC FeMn towards SiMn and refined alloys of both.
Low carbon SiMn with 20~30% Si is produced by upgrading standard SiMn alloy by the addition of Si wastes from ferrosilicon industry. The Mn(-Fe)-Si-C system is an important metallic system in production of SiMn. Graphite is the stable phase in the lower Si range. When the Si content is raised to a certain value at a fixed temperature, the coexistence point is reached where the liquid alloy will be in equilibrium with both graphite and silicon carbide (SiC). At Si-contents above this point, SiC will become the stable phase. Therefore, the addition of Si decreases the solubility limit of C in SiMn alloy melt. Notwithstanding this well-known thermodynamic information, there are few experimental data for understanding the refining mechanism of carbon (or SiC) from SiMn melt.
Based on the above backgrounds, in the present study, the dissolution of SiC particle at 1600oC in the CaO-SiO2-MnO slag was observed in situ by means of confocal scanning laser microscopy in order to make the determination of dissolution mechanism. The SiC particle is initially wetted by molten slag from the outer surface and the wetting between SiC and slag phase is more dominant in the composition of higher CaO/SiO2 ratio. When the SiC particle is wetted by molten slag, the gas bubbles that are mainly CO gas is generated by the reaction between SiC and MnO in slag phase and are continuously evolved at the wetted area, which is pronounced as the CaO/SiO2 ratio increases. The dissolution of SiC particle in the slag through the reaction with MnO is enhanced in the composition of higher CaO/SiO2 ratio not only due to greater thermodynamic driving force but also due to accelerated mass transport kinetics.
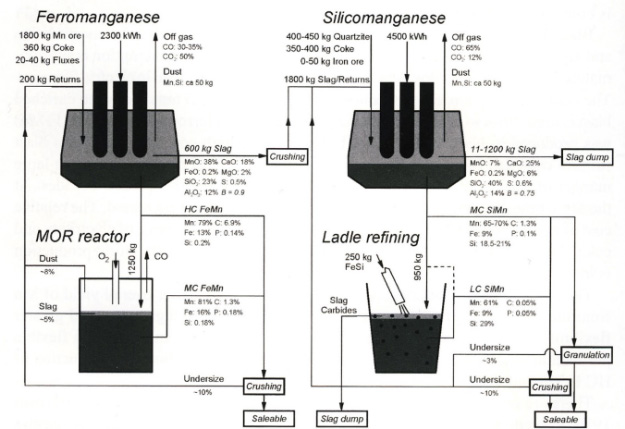
Duplex production of HC FeMn and SiMn, with refining processes
(reproduced from 'Production of Manganese Ferroalloys', Olsen et al., SINTEF and Tapir academic press, 2007)
(reproduced from 'Production of Manganese Ferroalloys', Olsen et al., SINTEF and Tapir academic press, 2007)
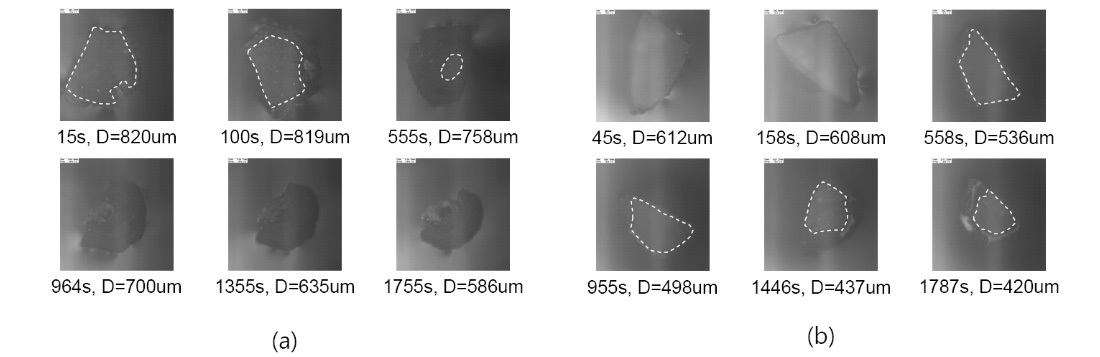
Dissolution sequence of SiC particle in (a) CaO-SiO2-10%MnO (C/S=1.0) and (b) CaO-SiO2-20%MnO (C/S=0.5) slags at 1873 K under a purified Ar atmosphere (Unwetted area is the inner part of the dashed line).
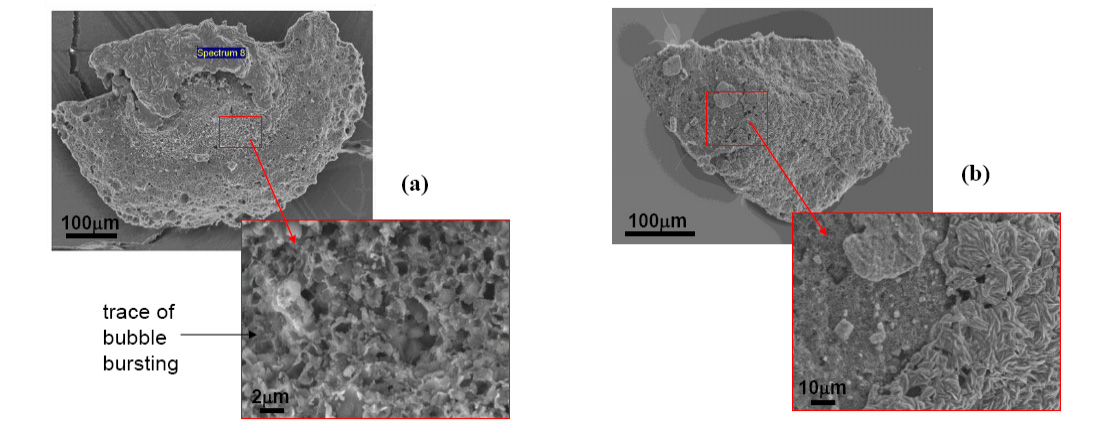
Surface morphology of SiC particle with (a) CaO-SiO2-10%MnO (C/S=1.0) and (b) CaO-SiO2-20%MnO (C/S=0.5) slags at 1873 K.
Carbide Capacity of CaO-SiO2-MnO Slag for the Production of Manganese Alloys
(Park et al.; ISIJ Int., 2010, vol.50, p. 1078)
There are several studies for the measurement of carbon solubility of metallurgical slags as carbide or carbonate according to oxygen partial pressure. Based on the previous works, one can conclude that the stable ionic form is carbide under reducing conditions that is in correspondence to the manganese alloys production. The solubility of carbide and thus carbide capacity generally increases with increasing basicity in the lime-based silicate, aluminate, and aluminosilicate melts with and without fluorspar, whilst there are some experimental results for an increase in the carbon solubility as the content of acidic oxides (SiO2 and B2O3) increases.
Even though there are some experimental results for the solubility of carbon in the lime-based slags, the carbide capacity of the MnO-containing slag is hardly found. The only system containing MnO in view of carbon solubility is the BaO-MnO flux, where the carbon solubility increased with increasing content of BaO not only due to a basic characteristic of BaO but also due to a strong ionic attraction between Ba2+ cation and carbide anion.
Therefore, in the present study, the carbide capacity of the CaO-SiO2-MnO slag, which is the main system produced during Mn alloys processes, through the wide composition region has been measured at 1773 K to understand the effective slag composition on the solubility of carbon in molten slags during SiMn production processes.
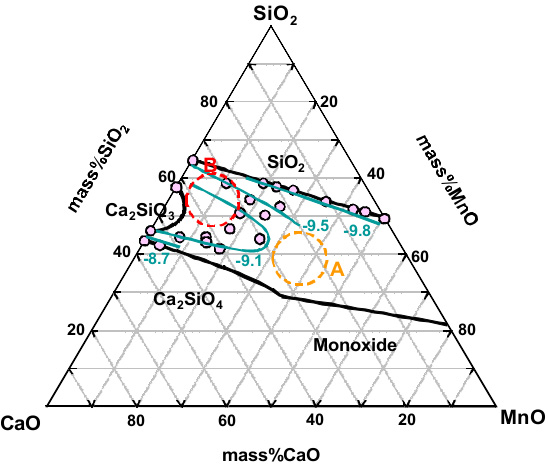
Iso-carbide capacity lines in the CaO-SiO2-MnO slag at 1773 K. Numerical values represent the 'log capacity'. A; HCFeMn slag. B; SiMn slag.