Research
home
Fundamental Research for Producing High-Purity & High-Cleanliness Stainless Steels
Refining of High-Mn Steels for Generation Applications
Applications of Computational Thermodynamics for Producing High-Clean Steels ; Focusing on Smart Manufacturing
Novel Manufacturing Processes for Advanced High-Entropy Alloys
Grain Refinement of Macro-& Microstructure of Steels using Non-Metallic Inclusion
Zn-AI-Fe Dross Formation Mechanism in Hot Dip Galvanizing Bath for Producing Advanced Automotive Sreels
Physical Chemistry of MnO-base Slags for Producing High-Functional Manganese Ferroalloys
Viscosity-Structure Relationship of Molten Slags and Glasses
High Temperature Physical Chemistry of Metals and Slags
Characterization of Chemical Reactions at Slag-Refractory Interface in High Temperature Reactors
Extraction and Purification of Titanium and Its Alloys
Physical Chemistry of Molten Salts for Producing Magnesium and Zirconium
Recovery of Precious- & Rare Metals from Electric Wastes and Industrial By-products ;Foucusing on Circular Economy
Recovery of Precious- & Rare Metals from Electric Wastes
and Industrial By-products ; Focusing on Circular Economy
(폐기물과 부산물로부터 귀금속 및 희소금속 회수에 관한 기초연구 ; 순환경제의 구현 )
Effect of slag composition on the distribution and separation behavior of arsenic between CaO-based slag and liquid copper
(Jooho Park, Kim and Joo Hyun Park; J. Hazard. Mater., 2022, vol. 436, article no. 129154)
In recent decades, the manufacturing and mining industries have grown rapidly. However, this growth has caused unintended side effects, including environmental issues. In particular, the elution of hazardous elements, such as arsenic (As), has caused various problems such as soil/water contamination and adverse health effects; thus, studies are being conducted around the world to support sustainable development by reducing the environmental pollution caused by these toxic residues. The removal and stabilization of arsenic through the use of slag at high temperatures is a focus of the present study.
Therefore, it is necessary to quantitatively investigate and optimize the effect of slag composition on the thermodynamic behavior of As. Also, the tendency of As segregation in slag should be investigated. In the present study, the distribution behavior of As between molten copper and the CaO-SiO2-Fe2O3-MgO-Na2O slag over a wide range of slag compositions was investigated. The study aimed to quantitatively reveal the effect of slag composition changes, including additives such as CaO and Na2O, on As control not only in the primary copper smelting processes but also in the secondary resources recycling processes employing black copper as raw materials feedstock.
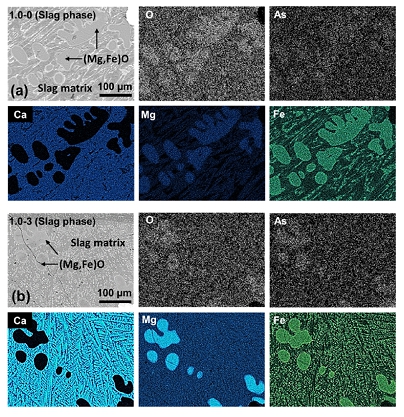
Representative EPMA mapping image for (Mg,Fe)O phase in slag which shows As segregation and enrichment phenomenon: (a) C/S= 1.0 and Na2O=0%, (b) C/S=1.0 and Na2O=3%.
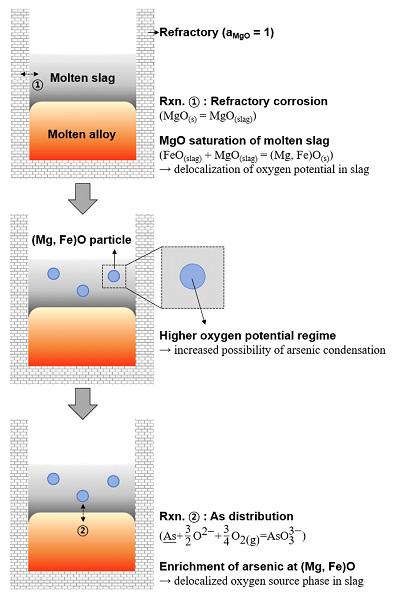
Arsenic distribution and segregation mechanism during slag-metal reaction and solidification procedure.
Effect of pyro-processing conditions on impurity removal and precious metal enrichment in waste printed circuit board (WPCB) recycling process
(Heo, Jooho Park and Joo Hyun Park; Resour. Conserv. Recycl., 2022, vol. 179, article no. 106068)
With rapid technological innovations and market expansion, the amount of waste electrical and electronic equipment (WEEE) as e-waste increases rapidly in the past decades. According to “The Global E-waste Monitor 2020” report, approx. 53.6 million tons (Mt) of e-waste (excluding PV panels) was generated, or 7.3 kg/capita in 2019. It is estimated that the amount of e-waste generated will exceed 74 Mt in 2030. Thus, the global quantity of e-waste is increasing at an alarming rate of almost 2 Mt/year. In 2019, e-waste was generated in the order of continents Asia (24.9 Mt or 5.6 kg/capita), America (13.1 Mt or 13.3 kg/capita), Europe (12 Mt or 16.2 kg/capita), Africa (2.9 Mt or 2.5 kg/capita), and Oceania (0.7 Mt or 16.1 kg/capita). However, e-waste collection and recycling rate was still lower than 12% except for Europe, which is the highest the rate (42.5%).
In this study, the effect of O2-blowing conditions and slag compositions on the removal rates of Si and Fe, as representative impurities in crude copper metal, and the enrichment ratio of Au and Ag are the primary focus by simulating smelting operation of WPCBs recycling in a laboratory scale. This study provides a guide how to optimize pyrometallurgical recycling process with respect to WPCBs for maximizing the enrichment of Au and Ag during oxygen refining at high temperatures based on the fundamental thermodynamic and thermophysical properties of slag.
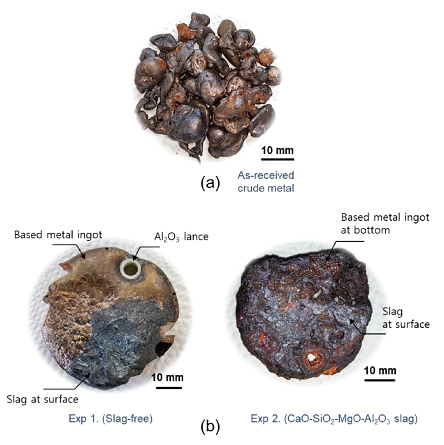
Pictures of (a) as-received crude metal (b) final metal ingots for Exps. 1 and 2.
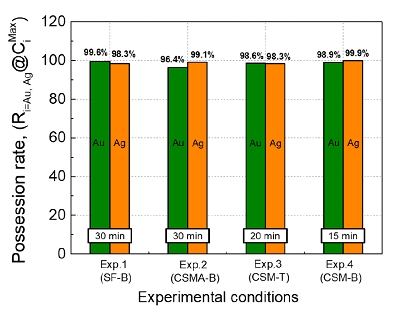
Possession rate at different experimental conditions.
Effect of Oxygen Blowing on Copper Droplet Formation and Emulsification Phenomena in Converting Process
(Jooho Park, Lee and Joo Hyun Park; J. Sustain. Metall., 2021, vol. 7, pp. 831-847)
Traditionally, various pyrometallurgical refining processes of scrap or ore using reactions between the gas, slag, and metal have been developed to produce target metals with a desirable composition. In addition, several special treatment procedures are also used to produce high grade ingots. For instance, in the high-grade copper production, in order to manufacture the electrolytic copper, an electro-refining process is performed after converting and slag cleaning, followed by the fire refining process. However, some critical impurities may not be removed in the converting process. In particular, iron adversely affects the cathode and acts as a factor in deteriorating the quality of the electrolyte solution. Therefore, it is necessary to thoroughly remove such impurities in the converting process to result in an economical yield. The relevant issues must be taken into account both in the primary smelting and converting processes using the copper concentrates and in the smelting process of secondary sources such as e-waste and/or black copper scrap. To achieve this goal, as mentioned above, the oxidative impurities are removed through the oxygen blowing at high temperatures.
The present research investigates the effect of the interfacial state on emulsification phenomenon that can occur when oxygen is over-injected through the process of removing impurities in crude copper melt and changes of the accompanying physicochemical phenomena. Through this study, the understanding of complex phenomena due to the physical and chemical effects of gas injection in gas-slag-metal reactions can be improved. In addition, it will be helpful to provide the insight to solve the problems related to the productivity in the recycling process of secondary copper scrap (i.e., black copper) as well as in the primary copper smelting process.

Schematic diagram of the oxygen blowing method by using alumina lance.
Massive recycling of waste mobile phones: Pyrolysis, physical treatment, and pyrometallurgical processing of insoluble residue
(Park et al.; ACS Sustain. Chem. & Eng., 2019, vol.7, pp.14119-14125)
Waste of electrical and electronic equipment (WEEE) has diversified due to the rapid development of the information technology (IT) industry. Specifically, a significant amount of mobile phones are thrown away because technical trends lead to the faster replacement of goods. The reuse or repair of mobile phones has long been in decline due to rising product complexity and shortened life cycles. Unlike general waste, waste mobile phones (WMP) include various heavy metals and hazardous substances. Lead, cadmium, mercury, PVC, and halogenated flame retardants are examples of those that pollute the environment. Mobile phones also contain significant amounts of resource materials derived from precious metals, carbonaceous materials, and inorganic parts. Valuable metals can be recovered from the lead frame (copper), solder (lead and tin), case (iron and aluminum), and IC chip (gold, silver, and palladium), which particularly increases the recycling rate of mobile phones.5 Among the various parts, printed circuit boards (PCBs) are considered to be essential to the urban mine industry due to integrated platinum group metals (PGMs). The global recycling of waste PCBs is mainly concentrated in Asia. The current recycling status of PCBs in China and South Korea were reviewed in recent publications.
The smelting treatment of insoluble residue was mainly covered to simulate the recovery procedure of precious metals in the molten state. Slag composition was controlled by incorporating different compositions of synthetic fluxes. Recovery rate was significantly influenced by the terminal velocity of metal particles in the liquid slag in association with slag viscosity and silicate structures.
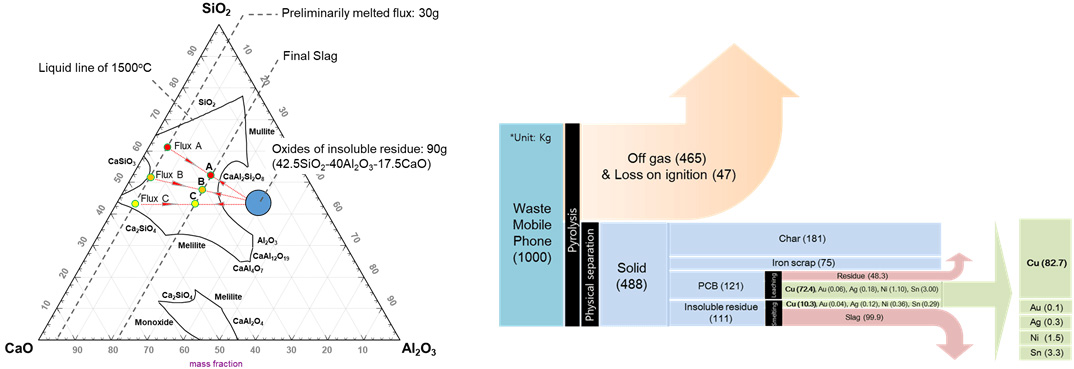
Oxide composition of insoluble residue, different fluxes (A, B, and C), and prospected slag compositions illustrated in the CaO−Al2O3−SiO2 ternary phase diagram at 1500 °C.
Material flow from experimental results calculated as complete leaching of PCB and smelting process of insoluble residue through slag C.
Thermodynamics of gold dissolution behavior in CaO-SiO2-Al2O3-MgOsat Slag System
(Han, Swinbourne and Park; Metall. Mater. Trans. B, 2015, vol.46B, pp.2449-2557)
Gold is a bright yellow, dense, soft, malleable, and ductile metal and has been a valuable and highly sought-after precious metal for coinage jewelry and other arts since long before the beginning of recorded history. Physically, gold is the most ductile of all metals, is a good conductor of heat and electricity, and reflects infrared radiation strongly. Chemically, it does not react with water, dry or humid air, and most corrosive reagents, so these are the reasons why it is well suited for use in coins and jewelry and as a protective coating on other more reactive metals.
Consequently, in the present study, gold solubility in the CaO-SiO2-Al2O3-MgOsat slag system was measured at 1773 K at pO2 = 10-10 atm to pO2 = 10-8 atm using a CO–CO2 gas mixture over a wide range of compositions, i.e., 8 to 40 mass pct CaO, 26 to 50 mass pct SiO2, and 0 to 36 mass pct Al2O3, to determine the dissolution mechanism of gold in the calcium silicate-based slags.
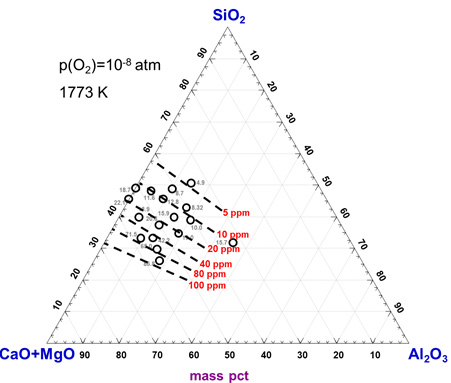
Iso-gold solubility contours in the CaO-SiO2-Al2O3-MgOsat system at 1773 K.
Thermodynamics of Indium Dissolution Behavior in FeO-bearing Metallurgical Slags
(Han and Park; Metall. Mater. Trans. B, 2015, vol.46B, pp.235-242)
Indium (In) represents a minor percentage of the earth’s crust. Its concentration is comparable to that of silver, which is about 0.1 mass ppm, and ranges from 50 to 200 ppb in the earth’s crust. The average indium content in zinc deposits ranges from less than 1 to 100 ppm. Indium is usually produced as a minor by-product in the lead and zinc smelting and refining processes. It is a rare and valuable metal that is used in a variety of industrial applications, such as liquid crystal displays (LCDs), semiconductors, low-temperature solders, infrared photodetectors, and solar cells.
Low-cost FeO-bearing metallurgical slags are more interesting than synthetic CaO-SiO2-Al2O3 slag for pyrometallurgical processing of In-containing waste materials. Nevertheless, the indium dissolution behavior in FeO-bearing metallurgical slags is controversial. Because the fayalite slags can be easily obtained from copper smelters after smelting, the FeO-bearing slag system can potentially be used as an economic flux in pyro-recycling. Therefore, in the current study, indium solubility in the FeO-SiO2-Al2O3-CaO-MgOsat slag system was measured at 1573 K using a CO-CO2 gas mixture over a wide range of compositions to determine the dissolution mechanism of indium in FeO-bearing slags.
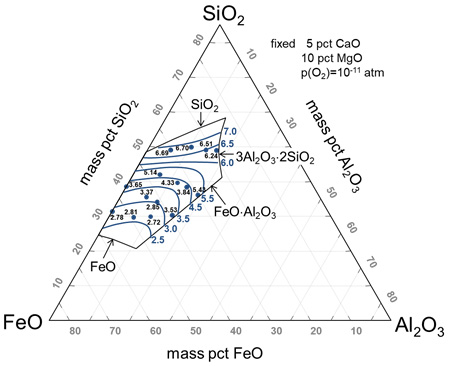
Iso-indium solubility contours in the FeO-SiO2-Al2O3-5CaO-MgOsat slag system at 1573 K.
Dissolution Behavior of Indium in CaO-SiO2-Al2O3 Slag
(Ko and Park; Metall. Mater. Trans. B, 2011, vol.42B, pp. 1224-1230)
Indium is usually produced as a minor by-product of Pb and Zn smelting and refining processes. Primary production peaked at just over 600t in 2007, falling back to around 520t in 2009. China has emerged as the world’s leading producer of indium, as its output has increased from 73t in 1999 to a peak of 320t in 2006. In 2009, China accounted for just over half of the total world output of indium. Growth in demand has prompted an increase in recycling; indium is most commonly recovered from ITO sputtering targets and LCD screens, which are its main applications. It is also used in low melting point alloys and compound semiconductors. Recently, the pyro- and hydrometallurgical recycling of indium-containing electric parts and dental materials has been termed “urban mining” due to the very high cost and scarcity of indium. However, the mechanism of indium dissolution into slags and fluxes, which is crucial for determining the operating parameters, is not fully understood.
The literature contains only two experimental studies on the distribution of indium between Pb and slags. The dissolution mechanism of indium, however, was not established in these experiments.
In the present study, therefore, the solubility of indium in the CaO-SiO2-Al2O3 slag was measured at 1773 K (1500 oC) and under a highly reducing atmosphere over a wide range of compositions within the liquid area in the slag system in order to elucidate the dissolution mechanism of indium in metallurgical slags under reducing conditions.
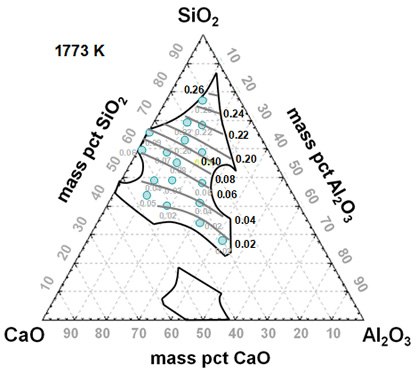
Iso-indium solubility contours in the CaO-SiO2-Al2O3 system at 1773 K.