Research
home
Fundamental Research for Producing High-Purity & High-Cleanliness Stainless Steels
Refining of High-Mn Steels for Generation Applications
Applications of Computational Thermodynamics for Producing High-Clean Steels ; Focusing on Smart Manufacturing
Novel Manufacturing Processes for Advanced High-Entropy Alloys
Grain Refinement of Macro-& Microstructure of Steels using Non-Metallic Inclusion
Zn-AI-Fe Dross Formation Mechanism in Hot Dip Galvanizing Bath for Producing Advanced Automotive Sreels
Physical Chemistry of MnO-base Slags for Producing High-Functional Manganese Ferroalloys
Viscosity-Structure Relationship of Molten Slags and Glasses
High Temperature Physical Chemistry of Metals and Slags
Characterization of Chemical Reactions at Slag-Refractory Interface in High Temperature Reactors
Extraction and Purification of Titanium and Its Alloys
Physical Chemistry of Molten Salts for Producing Magnesium and Zirconium
Recovery of Precious- & Rare Metals from Electric Wastes and Industrial By-products ;Foucusing on Circular Economy
Zn-Al-Fe Dross Formation Mechanism in
Hot Dip Galvanizing Bath for Producing Advanced Automotive Steels
(차세대 자동차용 아연도금강판 제조기술 개발을 위한 용융 Zn 중 Zn-Al-Fe계 금속간화합물 (dross) 생성기구 규명)
Effect of initial iron content in a zinc bath on the dissolution rate of solid iron during hot dip galvanizing process
(Lee, Pak and Park; Metall. Mater. Trans. A, 2017, vol.48A, pp.1788-1796)
During the hot dip galvanizing process, dross particles, which are intermetallic compounds of the Zn-Fe-Al system, affect the surface quality of the steel sheet. Thus, the changes in Fe or Al concentration in molten zinc have a significant impact on the production of high-quality steels. When a steel sheet is immersed in a zinc bath, dissolved iron creates the Fe-Zn and Fe-Al intermetallic compound layer on the surface of the steel sheet. Additionally, dissolved iron from the steel sheet promotes the precipitation of d (FeZn10Alx), z (FeZn13), and h (Fe2Al5Znx) phase dross particles in molten zinc.
Even though previous studies have predicted the dissolution rate of Fe in practical conditions, the mechanism of iron dissolution from the steel sheet has not been fully clarified. Thus, the objective of the present work was to confirm the mechanism of iron dissolution as well as the effect of the initial Fe content in the Zn bath on the dissolution rate of iron using a finger rotating method (FRM), in which the iron cylinder was rotated with a fixed revolution per minute (rpm) rather than a simple dipping method in order to qualitatively simulate the dynamic galvanizing operation conditions.
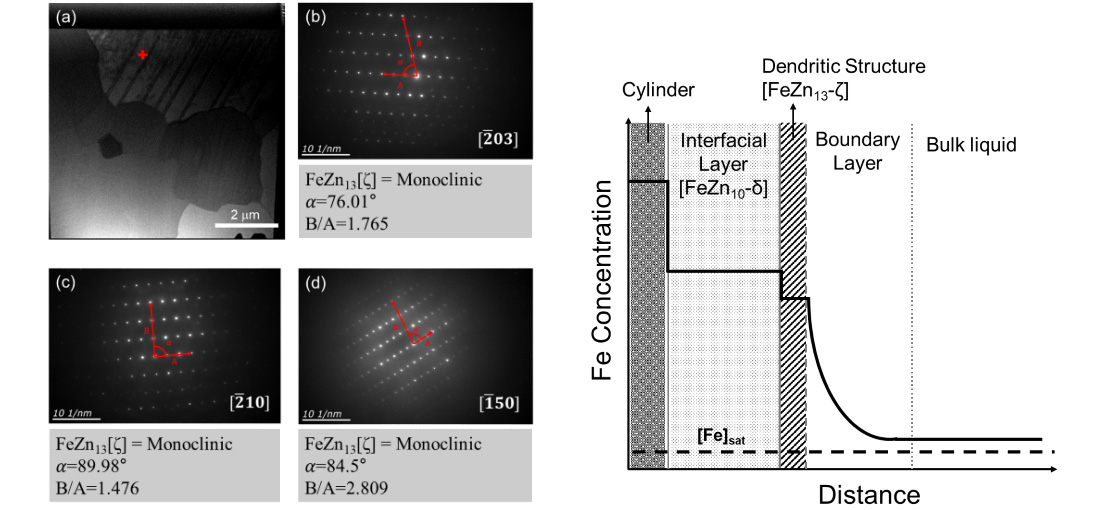
(a) FIB sample image of the FeZn13 (ζ) dendrite layer formed at the surface of the iron cylinder in the system of [Fe]o=300 ppm at 360 min and (b) to (d) diffraction pattern of the cross bar position in ‘(a)’.
Schematic diagram of the concentration profile of iron from the iron cylinder side to the bulk zinc melt.
Influence of Aluminum on the Formation Behavior of Zn-Al-Fe Intermetallic Particles in Zinc Bath
(Park et al.; Metall. Mater. Trans. A, 2012, vol.43A, pp. 195-207)
Zinc coatings are predominantly used to improve the aqueous corrosion of steel by providing barrier protection as well as galvanic protection. One of the typical processing methods used in producing Zn coatings is hot-dip galvanizing (HDG), i.e. the immersion of a steel sheet in a liquid bath of Zn or Zn alloy, by batch or continuous processing, the latter being more advantageous for coiled products. The growing importance of HDG coatings on automotive parts has led in recent years to studies on the mechanisms of their formation on IF steel substrates as well as high strength TRIP and TWIP steels of high strength and good formability.
DINC HUH, is with ne with teh ment Team, Dross in the Zn pot can be classified by oxide type (Zn and/or Al) and intermetallic compound type (Zn-Fe and Fe-Al). The latter type tends to cause dross problems and forms in the Zn pot when Al and Fe are present in concentrations above the solubility limits. Specifically, problematic intermetallic compounds have been identified as Fe2Al5Znx (h phase) “top” or “floating” dross as well as FeZn7 (d1 phase), FeZn10Alx (d phase) and FeZn13 (z phase) “bottom” dross particles.
A number of studies have investigated the phase equilibria of Zn-Al-Fe ternary systems, and stable and metastable phases in dross formation. There have been several studies on the kinetics of dross particle formation including estimation of the diffusion coefficients of Al and Fe in a Zn bath, modeling of dissolution of Fe from steel sheet, and Al uptake. However, compared to the thermodynamic and kinetic modeling studies in the formation behavior of dross particles, there have been few experimental studies attempting to elucidate the dross particle (morphology and phase) evolution during galvanizing processes.
Based on these preceding studies, the effect of Al content on the formation behavior of dross particles has partly been unveiled. However, it is also important to take into account the formation behavior of dross particles under conditions of pouring the premelted Zn-Al ingot into the bath, in which the Al content is locally increased and thus affects the very initial stage of dross formation. In the present study, the shape, size, and composition of dross particles as a function of Al content at a fixed bath temperature were investigated for Al added to the premelted Zn-Fe melt using a sampling methodology.
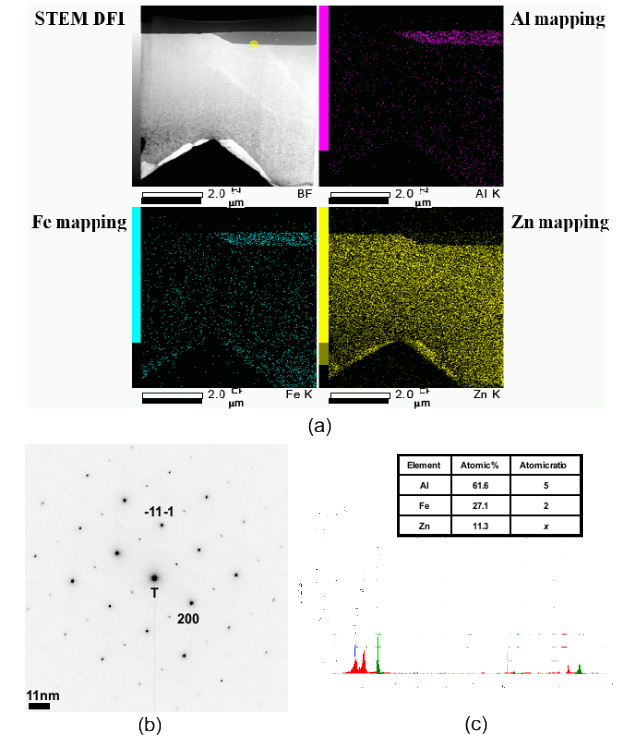
TEM element mapping of dross phase (a) and phase identification by diffraction pattern (b) and EDS data (c).
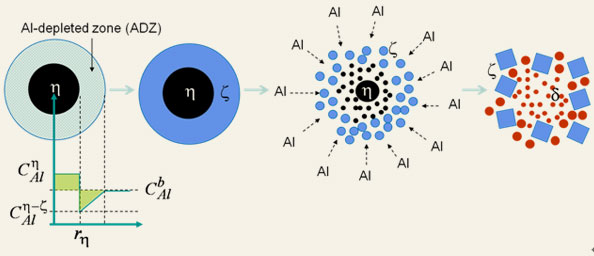
Sketch of the “Al-Depleted Zone (ADZ)” mechanism for evolution of dross particles from the “h ® h+z ® d” phase transformations.