Research
home
Fundamental Research for Producing High-Purity & High-Cleanliness Stainless Steels
Refining of High-Mn Steels for Generation Applications
Applications of Computational Thermodynamics for Producing High-Clean Steels ; Focusing on Smart Manufacturing
Novel Manufacturing Processes for Advanced High-Entropy Alloys
Grain Refinement of Macro-& Microstructure of Steels using Non-Metallic Inclusion
Zn-AI-Fe Dross Formation Mechanism in Hot Dip Galvanizing Bath for Producing Advanced Automotive Sreels
Physical Chemistry of MnO-base Slags for Producing High-Functional Manganese Ferroalloys
Viscosity-Structure Relationship of Molten Slags and Glasses
High Temperature Physical Chemistry of Metals and Slags
Characterization of Chemical Reactions at Slag-Refractory Interface in High Temperature Reactors
Extraction and Purification of Titanium and Its Alloys
Physical Chemistry of Molten Salts for Producing Magnesium and Zirconium
Recovery of Precious- & Rare Metals from Electric Wastes and Industrial By-products ;Foucusing on Circular Economy
Characterization of Chemical Reactions
at Slag-Refractory Interface in High Temperature Reactors
(고온 반응기 (소각로, 정련로, 용해로 등) 내 슬래그/내화물간 계면반응 특성 규명)
Interfacial reactions between magnesia refractory and electric arc furnace (EAF) slag with use of direct reduced iron (DRI) as raw material
(Heo and Park; Ceram. Int., 2022, vol. 48, pp. 4526-4538)
In the electric arc furnace (EAF) process, the most common form of scrap substitute material is direct reduced iron (DRI). DRI is produced from a combination of lump and pelletized ore reduced in a shaft furnace (e.g., MIDREX furnace) by reformed natural gas. DRI has several advantages including no unwanted tramp elements, a uniform density and shape, a relatively high yield and purity of carbon, convenient charging using a pellet shaped material, lower raw materials cost and low CO2 emissions. However, using DRI inevitably increases EAF slag volume and changes slag composition due to gangue components such as SiO2 in the DRI. Slag composition deviates from the operating reference, and the substitution of scrap for DRI in the EAF process would affect the operational stability, energy consumption, refining ability of the slag, and reduce the refractory life time. Because the lifetime of the refractory is closely associated with the number of operating charges, it is necessary to minimize chemical/physical degradation of the refractory during the EAF process.
Few studies have investigated the effects of varying DRI content on the interfacial reactions between EAF slag and magnesia refractory. Experimental studies using commercial DRI are still scarce, preventing a full understanding of the slag/refractory interfacial reaction in the EAF process. Furthermore, no one has reported what factors (e.g., MgO solubility as a thermodynamic force and viscosity as a kinetic factor) should be controlled by comparing them. Therefore, in the present study, the interfacial reaction between the EAF slag (CaO-SiO2-FeO-MgO-Al2O3-MnO system) and the magnesia refractory was investigated as a function of DRI content (0, 10, 20, and 30 wt%). In addition, a schematic diagram of the slag/refractory interfacial reaction was proposed through experimental investigations and thermodynamic calculations.
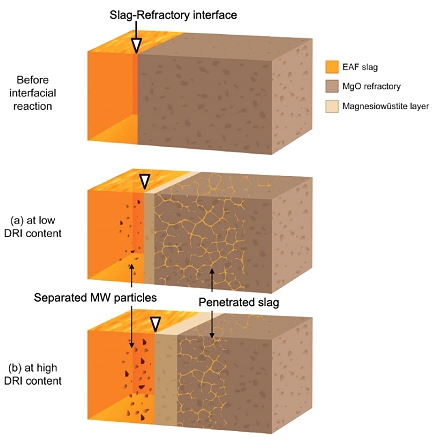
Schematic diagram of slag/refractory interfacial reaction phenomena comparing low and high DRI conditions.
Effect of fluorspar on the interfacial reaction between electric arc furnace slag and magnesia refractory: Competitive corrosion-protection mechanism of magnesiowüstite layer
(Park; Ceram. Int., 2021, vol. 47, pp. 20387-20398)
Use of direct reduced iron (DRI) as an alternative iron source in an electric arc furnace (EAF) steelmaking process has grown in popularity because DRI has no tramp elements, a uniform density and shape, relatively high yield and purity of carbon, charging convenience, lower raw materials cost, and low CO2 emissions. However, when DRI is used as an alternative iron source in the EAF process, the slag volume increases due to the gangue oxides in the DRI. In addition, the effect of acidic oxides (e.g., SiO2) in the gangue component reduces the refining efficiency of impurities, such as phosphorus. When fluorspar (CaF2) is added to FeO-containing slag, it has been known to improve the slag refining ability and the fluidity. Therefore, in EAF process using DRI, fluorspar is used as a fluxing material to minimize the increase in slag volume and maximize the refining efficiency. Recently, it was reported that CaF2 (~5 wt%) can improve the dephosphorization efficiency when DRI is used as a raw material in an EAF process.
Few studies have investigated the effect of CaF2 on the interfacial reaction between ‘FeO’-containing slag and magnesia refractory under dynamic conditions, and the refractory corrosion behavior is still unclear. Therefore, in the present research, the interfacial reaction between the CaO-SiO2-FeO-Al2O3-MnO-MgO-xCaF2 (CaO/SiO2=0.9-1.2, x=0-10 wt%) type EAF steelmaking slag and the magnesia refractory was investigated. In addition, a mechanism for refractory corrosion-protection was proposed through the investigation of slag-refractory interfacial reactions.
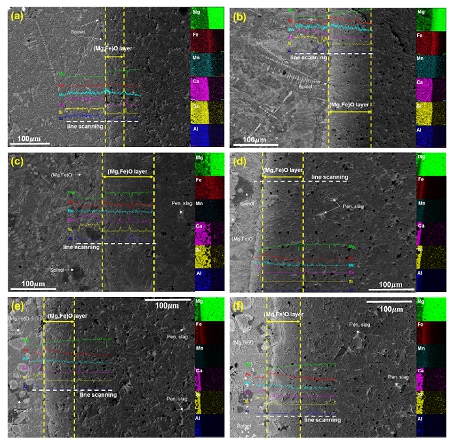
Slag/refractory interface for the post-mortem samples of (a) EAF slag (EAFS), (b) EAFS+20DRI, (c) EAFS+20DRI+3CaF2, (d) EAFS+20DRI+5CaF2, (e) EAFS+20DRI+7CaF2 and (f) EAFS+20DRI+10CaF2 (numbers represent wt%)
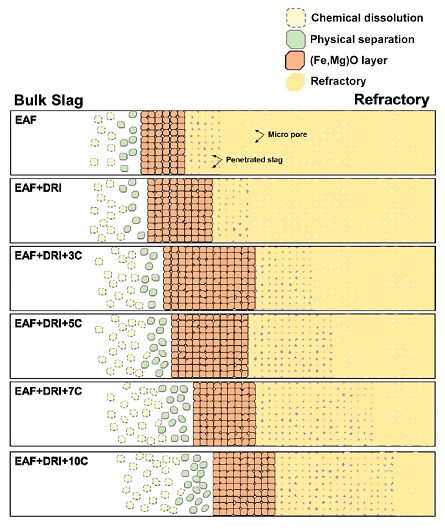
Conceptual sketch of the corrosion-protection mechanism by the slag-refractory interfacial reactions.
Interfacial reaction between magnesia refractory and “FeO”-rich slag: Formation of magnesiowüstitie protective layer
(Han, Heo and Park et al.; Ceram. Int., 2019, vol.45, pp.10481-10491)
In steel shops, intense reactions occur at the interfaces between the metal-slag-refractory phases and can occur in operating vessels such as electric arc furnaces (EAF), ladle furnaces (LF), and vacuum degassers (VD). The refractory is attacked by complex reactions including gas-slag-metal multiphase reactions, which occur simultaneously, and must have a superior resistance to thermal shock, mechanical abrasion, and chemical corrosion caused by slag under reducing and/or oxidizing atmospheric conditions. Magnesia-based refractories are widely used for LF or EAF due to their relatively high corrosion resistance and high temperature strength. Therefore, it is important to identify the reactions that occur between the magnesia-based refractory and various slag systems. Many studies have investigated the complex reactions between various slag systems and refractories with respect to corrosion mechanism. Lee and Zhang reviewed the corrosion mechanism in detail for various refractories used in melt shops including MgO-C, zirconium, spinel, and alumina.
Few studies have analyzed the interfacial reaction between “FeO”-rich slag and magnesia refractory, and simulation models for the slag-refractory reaction are still unclear. Therefore, in this study, we investigate the reaction between CaO-SiO2-Al2O3-xFeO-MgO-MnO (CaO/SiO2=1.2, x=20-50 wt%) slag and magnesia refractory. We also propose a new corrosion model of the slag-refractory reaction using the FactSage™7.0 software and compare the results to our experimental findings.
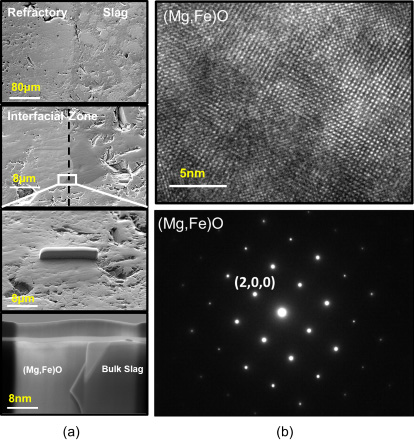
(a) Sample preparation using focused ion-beam method and (b) selected area electron diffraction pattern of (Mg,Fe)O phase.
Influence of CaF2 in calcium aluminate based slag on degradation of magnesia refractory
(Han, Kang, Shin, Chung and Park et al.; Ceram. Int., 2018, vol.44, pp.13197-13204)
Recently, demand for high-clean steel has increased rapidly. In order to produce high-clean steel, highly basic slag is required to maximize the desulfurization and deoxidation efficiency during the secondary refining processes, which can be achieved with the addition of lime (CaO). Magnesia based refractory, which is corrosion resistant to basic slag, is generally used as lining material during production. However, in the case of a highly basic slag (e.g. CaO/SiO2>1.5), increases in the apparent viscosity due to the precipitation of dicalcium silicate (Ca2SiO4) is a severe problem because it decreases the effective liquid fraction of slag. Moreover, the physicochemical properties of a slag become deteriorated, and there is a decrease in refining efficiency, which means slower desulfurization and deoxidation kinetics. To solve these problems, fluorspar (CaF2), which has low melting point (approx. 1693 K), is widely used to control the thermophysical properties of a slag. The role of fluorspar in decreasing the viscosity of molten aluminosilicate slags is well known. When fluorspar is added as a fluxing material to a highly basic slag, the melting point, and thus the apparent viscosity, of the slag decreases.
In the present study, MgO solubility was experimentally confirmed in conjunction with thermodynamic computations using FactSage™ (version 7.0) in order to constrain the effect of CaF2 on the solubility of MgO in the CaO-Al2O3-SiO2-MgO-xCaF2 (x=0–15 wt%) type ladle slag. Then, the effect of the thermophysical properties of the slag on the penetration depth into the MgO refractory was quantitatively evaluated under conditions of a fixed thermodynamic driving force for MgO dissolution, i.e., MgO saturation condition. Consequently, the influence of the thermophysical properties of the slag on slag penetration and refractory degradation was systematically evaluated.
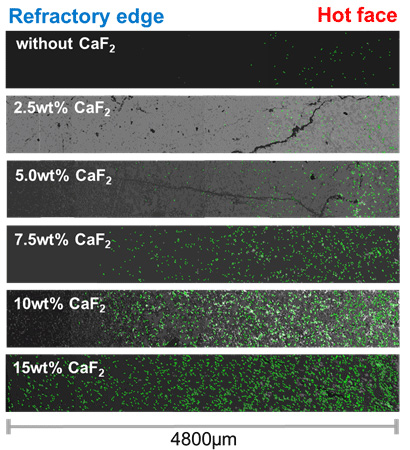
A BSE image transformed from the automatic image analysis (AIA) program as a change of CaF2 content.
Thermodynamic stability of spinel phase at the interface between alumina refractory and CaO-SiO2-CaF2-MgO-Al2O3-MnO slags
(Park et al.; J. Am. Ceram. Soc., 2015, vol.98, pp.1974-1981)
Dissolution of refractory oxides into silicate melts is of great interest for understanding in-service refractory wear. Hence, it is important to understand the interfacial reaction between refractories and slags at working temperatures. Oishi et al. reported that a boundary layer concentration gradient exists during dissolution of a solid ceramic phase into a liquid phase as the diffusion of components in the liquid phase varies. Because of this phenomenon, the component that has relatively fast mobility is enriched at the boundary layer and, thus, a specific compound can be formed at the interface between the liquid slag and solid refractory. In this case, the dissolution of the intermediate compounds, for example, CaO.2Al2O3 and CaO.6Al2O3, is very important.
Since understanding the formation behavior of the spinel phase at the interface between the refractory and calcium aluminosilicate melts is very important, the thermodynamic analysis of the stability of the spinel phase at the refractory-slag interface also should be further elucidated. Recently, a number of studies evaluating multicomponent ceramic systems have been performed, including refractory, glass, slag, and inclusion using FactSageTM (ESM Software, Hamilton, OH), which is a commercial thermochemical computing software package, and good agreement between experimental and computational results have been reported. Therefore, in this study, the interfacial reaction between the fused alumina refractory and the CaO–CaF2–SiO2–Al2O3–MgO–MnO melts was investigated to estimate the stability of the spinel phase based on computational thermodynamics under manufacturing conditions of Mn-containing steel, which has been recently issued due to its high performance with superior ductility and very high strength.
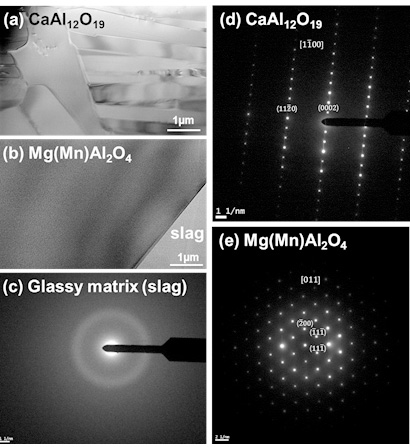
Bright field image of (a) CaAl12O19 and (b) Mg(Mn)Al2O4 + slag prepared using the FIB system and the SAED pattern of (c) glassy matrix slag, (d) CaAl12O19 and (e) Mg(Mn)Al2O4 in the Exp. #4 (C/S = 2.0).
Interfacial Reaction between Refractory Materials and Metallurgical Slags containing Fluoride
(Park, Suk, Jung, Guo and Blanpain; Steel Res. Int., 2010, vol.81, pp.860-868)
Dissolution of refractory oxides in silicate slags is of great interest for understanding in-service refractory wear. Chemical wear (corrosion) occurs as the refractory/slag system attempts to achieve equilibrium when the slag is not saturated with a refractory component. Even though extensive studies on dissolution of alumina (corundum), magnesia-carbon, magnesia-chromite, magnesia-alumina (spinel), in molten silicate melts have been the subject of many publications, the interfacial reactions between zirconia and dolomite refractories and silicate slags containing fluorine have not been explored intensively.
The study described herein is focused to reveal details of the interfacial reactions between CaO-SiO2-MgO-CaF2 slags and zirconia stabilized with MgO, fused magnesia, and dolomite refractories at high temperatures by employing various methodologies.
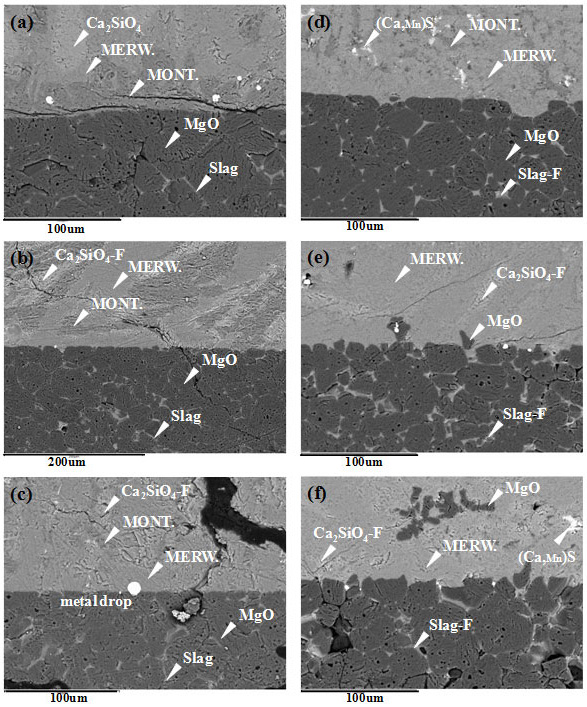
Magnesia refractory corroded by slag containing (a) 0, (b) 2.1, (c) 4.1, (d) 6.2, (e) 14.4, and (f) 21.7wt% CaF2.
Corrosion Behavior of Zirconia Refractory by CaO-SiO2-MgO-CaF2 Slag
(Suk and Park; J. Am. Ceram. Soc., 2009, vol.92, pp.717-723)
Zirconia has become one of the most industrially important high-temperature structural materials because of chemically and mechanically excellent properties. Along with high strength and toughness, ZrO2 also possesses good hardness, wear resistance, and thermal shock resistance. The most widely applied area of ZrO2 is the refractory ceramics for high-temperature process such as glass-melting furnace and a submerged entry nozzle (SEN) in continuous casting of steel. For glass-melting furnaces, the refractories used for the glass-contacting zone in furnaces must have high corrosion resistance to molten glasses. Because corrosion of refractory is greatly affected by the composition of the glasses, it is necessary to know the relation between glass compositions and refractory corrosion.
For continuous casting of steel, the refractory used for the SEN plays a very important role as it is the last refractory in contact with the liquid steel. Therefore, the quality of the steel products will be deteriorated or the casting process may fail unless SEN can withstand thermal shock or corrosion attack from the liquid steel and molten flux. Fluorspar (CaF2) is extensively used in steelmaking process in order to enhance slag fluidity and the rate of lime dissolution. The use of fluorspar is also considered to be harmful regarding refractory corrosion and environmental issues. However, no study was done concerning the microstructures of corroded interface of ZrO2 refractory according to the CaF2 content.
Consequently, it is very important and helpful to investigate the dissolution behavior of ZrO2 refractory focusing on the microstructure evolution with increasing CaF2 content in slag from the viewpoint of the degradation mechanism of refractory. This study will present experimental results showing the characteristics of corroded interface of ZrO2 refractory focusing on the effect of CaF2 concentration. Furthermore melting temperature and vaporization behavior of slag will be investigated in order to ascertain the corrosion phenomena of ZrO2 refractory with an increase of CaF2 content in slag.
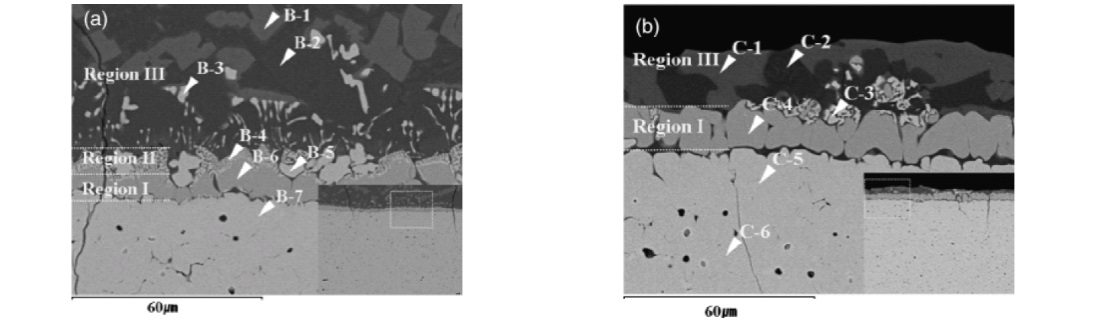
Microstructure of interface of ZrO2 refractory corroded by CaO-SiO2-MgO-7%CaF2 (a) and CaO-SiO2-MgO-19%CaF2 slag (b).
Formation of CaZrO3 at the Interface between CaO-SiO2-MgO-CaF2(-ZrO2) Slags and Magnesia Refractories: Computational and Experimental Study
(Park; Calphad, 2007, vol.31, pp.149-154)
Thermodynamic calculations and modeling have been useful in predicting the complicated phenomena such as the slag-metal-refractory reactions occurring in the ironmaking, steelmaking and casting processes without time-consuming experiments at high temperatures. Hence, the various thermodynamic models and the commercial packages have continuously been developed. Thermodynamic databases for steels, slags and solid solutions have been developed by Pelton et al. For example, FactSage accesses the F*A*C*T (Facility for the Analysis of Chemical Thermodynamics) database which incorporates the complex equilibria involving slags, steels, inclusions, refractories and gases. In this system, the Associate model for the molten steels and the modified quasichemical model for the molten oxides have been developed and the computation is based on the Gibbs energy minimization codes. Park investigated the microstructure of the CaO-SiO2-MgO-Al2O3(-CaF2) systems solidified during slow cooling, which are critical in understanding the inclusion systems in the stainless steelmaking processes, using SEM and an energy dispersive spectrometer (EDS). In this study, the phase equilibria at a specific temperature and composition were computed by employing the FactSage5.3TM thermochemical package, which were in good accordance to the measured results.
Hence, in the present study, the formation behaviour of the calcium zirconate (CaZrO3), which is an important refractory-protecting phase, at the interface between the CaO-SiO2-MgO-CaF2(-ZrO2) slags used in the AOD converter and the MgO refractories has been computed by employing the commercial thermodynamic software, FactSage5.4TM. Furthermore, the formation of CaZrO3 in the slags was experimentally confirmed using an XRD and SEM-EDS.
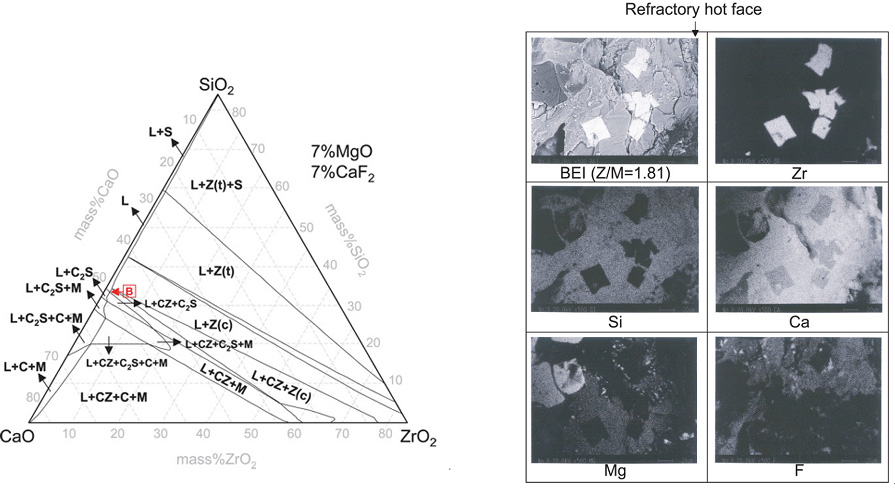
Computed phase diagram of the CaO-SiO2-ZrO2-7%MgO-7%CaF2 system at 1873 K.
ack scattered electron image of the slags (ZrO2/MgO=1.81) penetrated into the MgO refractory and the element mapping of the Zr, Si, Ca, Mg, and F.